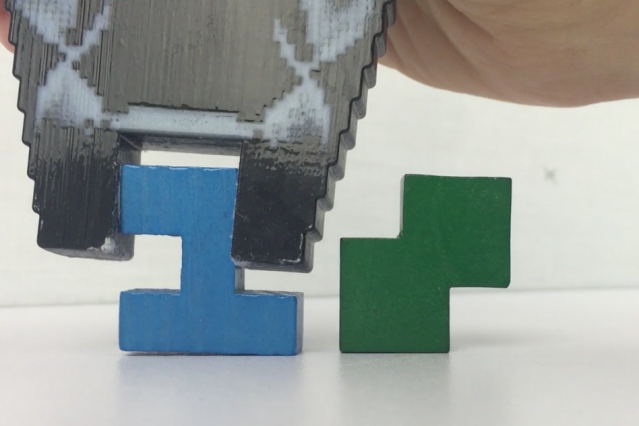
Modern 3D printers have a resolution of 600 dots per inch, which gives them the ability to ‘pack’ a billion tiny cubes – called voxels – of different materials into a volume measuring just 1.67 cubic inches.
This gives designers commensurate control of the objects’ physical properties — such as their density or strength – but also presents them with a very time consuming problem of evaluating the physical effects of every possible combination of even just two materials, especially in an object consisting of tens of billions of cubes.
To overcome this problem, researchers at MIT’s Computer Science and Artificial Intelligence Laboratory (CSAIL) have developed a new design system that catalogues the physical properties of a huge number of tiny cube clusters.
These clusters can then serve as building blocks for larger printable objects, allowing the system to take advantage of physical measurements at the microscopic scale, while enabling computationally efficient evaluation of macroscopic designs.
“Conventionally, people design 3D prints manually. But when you want to have some higher-level goal — for example, you want to design a chair with maximum stiffness or design some functional soft [robotic] gripper — then intuition or experience is maybe not enough,” said Bo Zhu, a postdoc at CSAIL and first author on the paper. “
“Topology optimisation, which is the focus of our paper, incorporates the physics and simulation in the design loop. The problem for current topology optimisation is that there is a gap between the hardware capabilities and the software. Our algorithm fills that gap.”
Bernd Bickel, an assistant professor of computer science at the Institute of Science and Technology Austria, said the design and discovery of structures to produce materials and objects with exactly specified functional properties was central for a large number of applications where mechanical properties are important, such as in the automotive or aerospace industries.
“Due to the complexity of these structures, which, in the case of 3D printing, can consist of more than a trillion material droplets, exploring them manually is absolutely intractable,” Mr Bickel said.
“The solution presented by Bo and colleagues addresses this problem in a very clever way, by reformulating it. Instead of working directly on the scale of individual droplets, they first precompute the behaviour of small structures and put it in a database.”
“Leveraging this knowledge, they can perform the actual optimisation on a coarser level, allowing them to very efficiently generate high-resolution printable structures with more than a trillion elements, even with just a regular computer,” Mr Bickel concluded.
The research was supported by the U.S. Defence Advanced Research Projects Agency’s SIMPLEX program.
For more detailed information on MIT’s new design system click here.