In 2012, the manufacturing industry was one of the four industries in Australia which recorded the highest incidence rates for workers’ compensation claims due to work-related injuries. In 2010-11, out of the 929,520 manufacturing workers in Australia, more than 19,420 brought forth serious claims for workplace injuries.
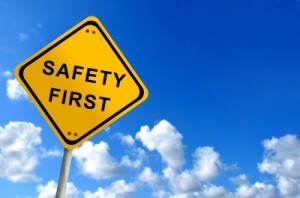
According to data from SafeWork Australia, work-related injury and illness cost the country about $60.6 billion, representing 4.8% of the GDP. A typical serious workers’ compensation claim involves four weeks of absence from work.
These figures have prompted risk-management training provider SAI Global to come up with an online safety training course that satisfies the critical criteria for OHS hazard audits Online Auditing OHS Management Systems.
OHS specialist Ray Bedson has put together seven steps to reduce hazards in the manufacturing industry.
Mr. Bedson trains hundreds of employees every year through SAI Global and he says inadequate risk plans, which are mostly due to lack of expertise and resources, contribute to the increase the number of workplace injuries.
“Employers can’t ignore the risks to their employees – a shoulder injury can cost an organisation $400,000 in accident compensation and prosecution costs, and a back injury over $1 million,” says Mr. Bedson.
The seven steps introduced by Mr. Bedson are the following:
1. Commit – all employees must devote themselves to carrying out the plan and be on board for the long run. “A risk plan can’t be carried out once and put aside,” said Bedson. “In an organisation of 100 employees, a risk or OHS manager may need to commit 80 hours per month, while remaining employees may need to commit another 120 hours per month collectively,”
2. Communicate – encourage employees to be vocal about potential hazards and anything that makes them nervous, including operational changes. A good way to discover potential hazards is to follow and observe an employee’s work for several hours. This would provide valuable insight into potential hazards in the workplace. Bedson also encourages a once-a-month discussion with employees regarding incidents that may have happened.
3. Record – Bedson says a Workspace Inspection Checklist would be helpful in identifying hazards as any employee can keep track of his observation in his own area. “Writing it down makes it harder to ignore, and it lets your team know you’re considering solutions to any issues,” he said.
4. Prioritize – using a Hazard Identification, Risk Assessment & Control (HIRAC) format to score each risk from negligible to extreme allows organizations to prioritize their actions. Forms are available from industry associations, statutory Work Safe or Work Cover authority. These can be filled out by the HR, safety and OHS coordinators, and other personnel with sufficient knowledge in the matter.
5. Control and consult – Bedson suggests implementing a control which will eliminate risks altogether, or minimize them through engineering solutions such as noise reduction. “Consult again with employees to ensure everyone agrees. Getting them involved will help ensure they implement the controls when the time comes,” he recommended.
6. Monitor and review – to determine if the processes and controls are effective, Bedson advised that they should be reviewed at least once a month. If there seems to be no change in the number of incidents and the level of significance then it’s time to re-think the plan.
7. Train new employees – invest in the training and development of new employees who are particularly at risk because of their inexperience and their lack of awareness in controlling hazards. Bedson says not only will this protect your business financially and legally, more importantly it can save their lives.
As a final note Bedson says there is no “secret” to optimum workplace safety since it is actually the practical and simple OHS risk management systems that are the most effective.
“In my 30 years’ experience in the industry, best practice OHS-risk management plans identify existing known hazards, measure and rank them, and outline simple and practical controls. They are developed by managers who understand their workplace surroundings and received comprehensive training on implementing OHS management systems. Every plan should simplify company processes and bring them into real-life situations,” Bedson said.
SAI Global’s self-paced course can be accessed online from the most remote areas, making it ideal for location-based industries.
For more information about SAI Global’s OHS training, visit www.saiglobal.com/ohs