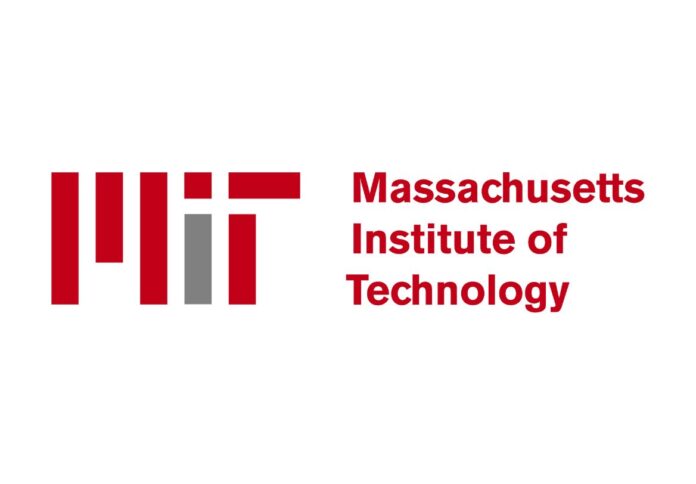
Engineers from the Massachusetts Institute of Technology have developed a new system that enables makers to incorporate sensors into gears and other rotational mechanisms with one pass in a 3D printer.
The researchers said that by incorporating sensors into rotational mechanisms, engineers could be able to create smart hinges that can detect when a door has been opened or motor gears that can communicate the rotational speed to a mechanic.
In particular, the engineers created a system called MechSense that enables a maker to use conductive 3D printing filament to 3D-print sensors directly into a mechanism’s moving elements.
This gives devices the ability to sense their angular position, rotation speed, and direction of rotation, as explained in a news release by the university.
To speed up the fabrication process, the researcher designed a SolidWorks plugin that automatically integrates sensors into a model of the mechanism, which could then be sent directly to the 3D printer for fabrication.
By using MechSense, engineers could rapidly prototype devices with rotating parts, like turbines or motors, while incorporating sensing directly into the designs.
This could be especially beneficial in designing tactile user interfaces for augmented reality environments, where sensing is important for tracking a user’s movements and interaction with items, the researchers said.
“A lot of the research that we do in our lab involves taking fabrication methods that factories or specialised institutions create and then making then accessible for people,” said Marwa AlAlawi, a mechanical engineering graduate student and lead author of a paper on MechSense.
“3D printing is a tool that a lot of people can afford to have in their homes. So how can we provide the average maker with the tools necessary to develop these types of interactive mechanisms? At the end of the day, this research all revolves around that goal,” AlAlawi further explained.
Researchers went on to say that a SolidWorks extension was used to streamline the user’s sensor integration process.
The technology then automatically adds sensor patches to the model once a manufacturer defines the rotating and stationary components of their mechanism as well as the centre of rotation.
The researchers used their system to prototype several devices, including a smart desk lamp that changes the colour and brightness of its light depending on how the user rotates the bottom or middle of the lamp.
They also produced a planetary gearbox, like those that are used in robotic arms, and a wheel that measures distance as it rolls across a surface.
AlAlawi and her colleagues intend to test various materials, as well as investigate ways to make their sensor design more resistant to outside noise and create printable sensors for other kinds of moving systems.
The study was funded in part by Accenture Labs.