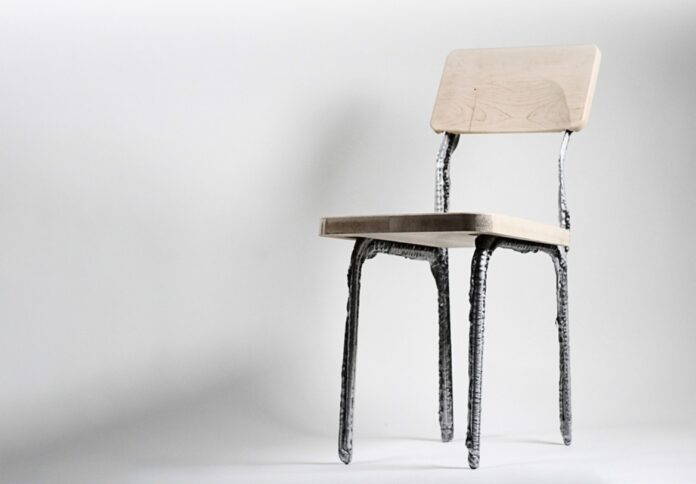
Scientists at the Massachusetts Institute of Technology (MIT) have introduced a technique dubbed liquid metal printing (LMP), enabling the rapid production of large-scale metal components such as table legs and chair frames within minutes.
The LMP process, developed by researchers at MIT’s Self-Assembly Lab, involves depositing molten aluminium onto a predefined path within a bed of tiny glass beads, the university said in a news release.
The molten metal quickly solidifies into a three-dimensional structure. MIT claims that LMP is at least 10 times faster than comparable metal 3D printing processes, with enhanced efficiency in the heating and melting of the metal.
According to researchers, while LMP prioritises speed and scale, it sacrifices resolution. However, this makes it ideal for applications in architecture, construction, and industrial design, where intricate details may not be crucial.
The technique also proves effective in rapid prototyping using recycled or scrap metal.
In a recent study presented at the Association for Computer Aided Design in Architecture Conference, MIT researchers showcased the versatility of LMP by printing durable aluminium frames and parts for tables and chairs.
These components were robust enough to withstand post-print machining, demonstrating the potential for combining LMP with high-resolution processes and additional materials to create functional furniture.
Skylar Tibbits, senior author of the paper introducing LMP and associate professor in the Department of Architecture, emphasises the innovation’s potential advantages.
“This is a completely different direction in how we think about metal manufacturing that has some huge advantages. It has downsides, too. But most of our built world — the things around us like tables, chairs, and buildings — doesn’t need extremely high resolution. Speed and scale, and also repeatability and energy consumption, are all important metrics.”
MIT’s LMP surpasses existing metal printing methods, such as wire arc additive manufacturing (WAAM), which can create large, low-resolution structures susceptible to cracking and warping due to remelting.
In contrast, LMP maintains the material in a molten state throughout the process, eliminating structural issues.
The MIT team built a specialised machine for LMP that melts aluminium, holds the molten metal, and deposits it at high speeds through a nozzle.
The large-scale parts can be printed in seconds, followed by rapid cooling of the molten aluminium in minutes.
Zain Karsan, lead author and PhD student at ETH Zurich, likens the process to “opening a faucet,” emphasising the challenge in controlling the high-speed procedure.
The researchers chose aluminium due to its common use in construction, cost-effective recycling, and efficient melting properties.
To facilitate the LMP process, MIT researchers experimented with various materials for the print bed, selecting 100-micron glass beads.
These beads, acting as a neutral suspension, withstand the high temperature of molten aluminium and enable quick cooling.
The research team acknowledges challenges, including nozzle clogging with ceramic nozzles and the need for consistent heating in the nozzle.
Despite these hurdles, researchers noted the potential applications of LMP are vast, to create a reliable machine capable of melting recycled aluminum for widespread use in metal manufacturing.
The research project received partial funding from Aisin Group, Amada Global, and Emeco, showcasing collaborative efforts in advancing the field of AM.