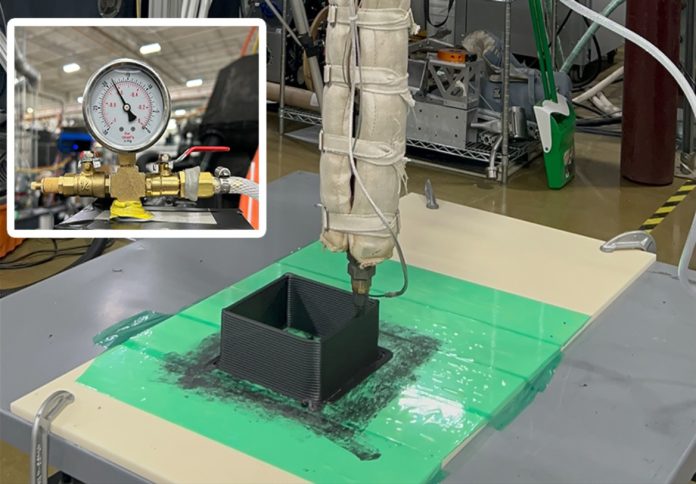
Researchers at the US Department of Energy’s Oak Ridge National Laboratory (ORNL) have developed a vacuum-assisted extrusion method that significantly reduces internal porosity in large-scale 3D-printed polymer parts, a development the lab says could improve part strength and accelerate industrial adoption of additive manufacturing.
According to ORNL, the new technique lowers porosity by up to 75 per cent, bringing void content to below 2 per cent in parts made with varying fibre content.
The process involves integrating a vacuum hopper into the extrusion system to remove trapped gases during printing, limiting the formation of internal voids – an issue that has long hindered the performance and reliability of components produced through large-format additive manufacturing (LFAM).
In a statement, ORNL said the innovation addresses a key obstacle in the use of fibre-reinforced thermoplastics, which are widely used in LFAM for their stiffness and low thermal expansion but are prone to intrabead porosity.
By minimising these voids, the method improves the mechanical properties of printed structures used in tooling and structural applications in aerospace, automotive, and defence sectors.
“Using this innovative technique, we are not only addressing the critical issue of porosity in large-scale polymer prints but also paving the way for stronger composites,” said Vipin Kumar, a researcher at ORNL. “This is a significant leap forward for the LFAM industry.”
ORNL noted that while the method is currently designed for batch processing, the lab has developed a patent-pending concept for applying vacuum-assisted extrusion in continuous deposition systems.
Future research will focus on adapting the technology for broader use in high-throughput manufacturing.