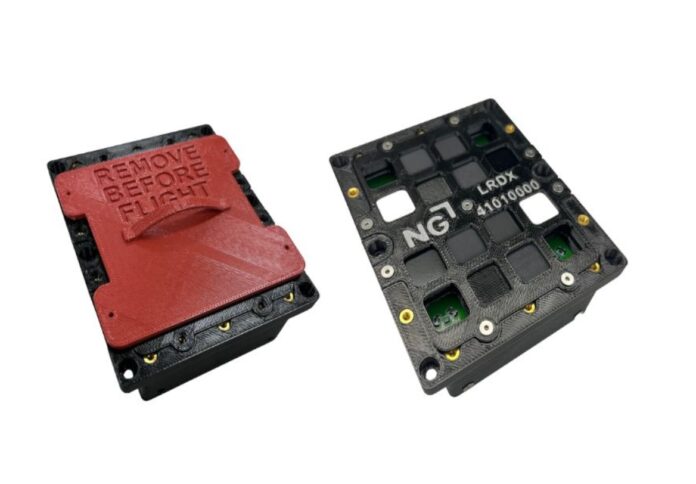
Additive manufacturing giant Stratasys announced its participation in an upcoming lunar mission aimed at evaluating the performance of 3D-printed materials on the surface of the moon.
This groundbreaking initiative forms part of Aegis Aerospace, Inc’s inaugural Space Science & Technology Evaluation Facility mission (SSTEF-1), a commercial space testing service developed under NASA’s Tipping Point program.
The SSTEF-1 project, spearheaded by Aegis Aerospace in Houston, Texas, focuses on advancing technology development for space infrastructure and capabilities in lunar and near-earth environments.
Stratasys’s experiments, sponsored by Northrop Grumman Corporation, mark a significant step forward in additive manufacturing’s role in space exploration, the company said in a media release.
As part of the mission, Stratasys will provide 3D-printed samples transported to the lunar surface by an unmanned lander within a carrier structure also 3D-printed by Stratasys.
The experiments, led by Northrop Grumman, will concentrate on three materials across two distinct trials.
The first experiment aims to evaluate the performance of a sample coupon part fabricated with Stratasys’ Antero 800NA FDM filament, infused with tungsten.
Antero 800NA, a high-performance PEKK-based thermoplastic renowned for its mechanical robustness and chemical resistance, is augmented with tungsten to provide shielding against hazardous radiation, including gamma rays and x-rays.
The second passive experiment will examine the behaviour of 3D-printed materials in space conditions.
It will involve Antero 840CN03 FDM filament, known for its electrostatic discharge (ESD) properties, alongside a novel ESD photopolymer developed by Stratasys partner Henkel for use with Stratasys’ Origin One 3D printers, designed specifically for high-heat environments.
This trial will subject coupon samples to lunar dust, low pressure causing outgassing, and rapid temperature fluctuations characteristic of the moon’s atmosphere.
Rich Garrity, chief industrial business officer at Stratasys, remarked, “Additive manufacturing is an important technology for space missions where every ounce of weight matters and high performance is essential.”
He continued, “This set of experiments will help us understand how to fully leverage 3D printing to keep people and equipment safe as we travel to the moon and beyond.”
The parts will be ferried to the lunar surface by an unmanned lander enclosed within a carrier structure 3D-printed from ULTEM 9085 thermoplastic, a material commonly utilised in commercial aircraft interiors, underscoring the adaptability and reliability of Stratasys’s solutions for space exploration efforts.