Tomcar Australia has ascribed its success in the manufacturing industry to Siemens PLM Software’s Solid Edge which helps the company save approximately $150,000 annually, according to a case study.
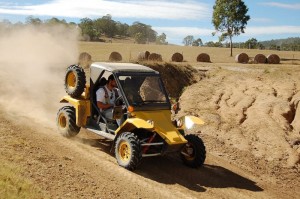
Established in 2005, Tomcar Australia manufactures all-terrain vehicles (ATVs) at its facility in Melbourne and uses Solid Edge in its entire design and development process.
David Brim, Chief Executive Officer and co-founder of Tomcar Australia says being a mid-sized company catering to a niche market means they do not have the same resources that other manufacturers have. Competing with big players that produce large-sized passenger vehicles has compelled them to rely on ‘Grade A technology’ to ensure detailed accuracy in every part they design.
Solid Edge helps the company achieve its production level of 5,000 units annually and helps them save a substantial amount of money.
“We recognize that to have a thriving business, we need to use products and technology that give us consistent, high-quality results without exception. Our engineers chose Siemens PLM Software as our technology provider, because Siemens met this requirement,” says Mr. Brim.
“Current auto market dynamics require companies to think about smarter and more cost-effective ways to design and manufacture,” says Brim. “One of the many reasons we are successful is because we have saved approximately $150,000 annually using Solid Edge.”
Solid Edge is a 3D design system that uses synchronous technology to accelerate design, make revisions faster, and enable better reuse.
To be able to compete in the market Tomcar Australia ensures that its time and materials are used efficiently so it was crucial for the company to utilize the software that would maintain accuracy throughout the whole process.
“Solid Edge was a natural choice for our engineers,” says Brim. “We use Solid Edge from sketching to modeling and the built-in finite element analysis (FEA) for simulation. It certainly helped us save on resources and time.”
With the help of Solid Edge, Tomcar Australia was able to produce its vehicles 12 months from finalizing the design, a time-frame virtually unheard of in the industry. The average time of design inception to vehicle production is 7 years says Mr. Brim.
“Completing the development of a reliable and performance-heavy product within a 12 month period requires intense activity and an extremely robust and efficient PLM infrastructure.”
“For our small team of developers and manufacturers, the Siemens PLM Software solution was a natural fit. Solid Edge has been the best software we’ve used, and the results we yield from using it continue to impresses us.”