Space technology company Rocket Lab has introduced the Rutherford engine that will act as the main propulsion system of its small satellite launch vehicle called Electron.
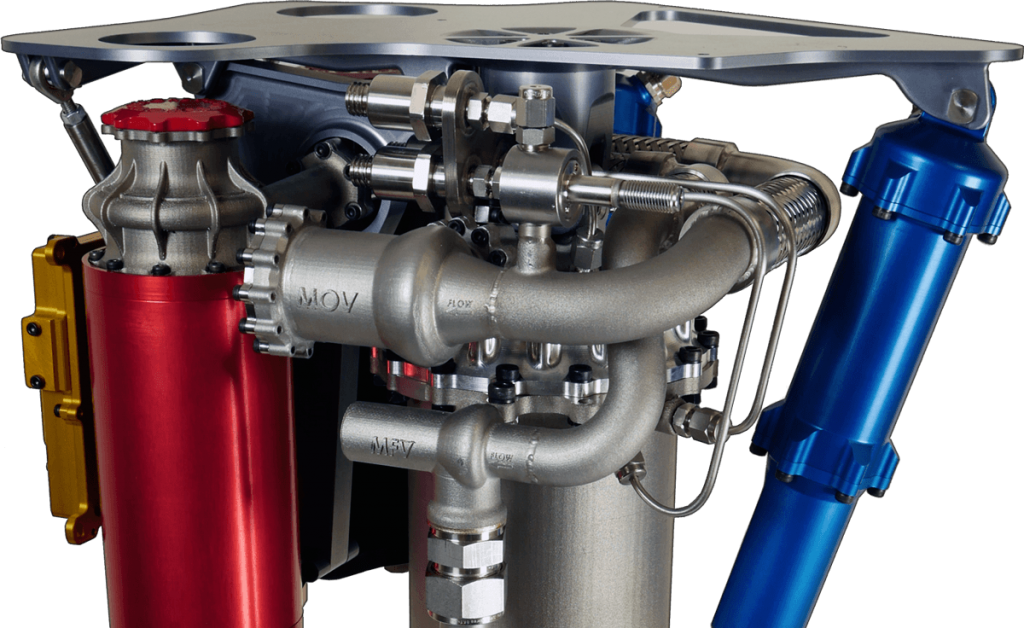
Image credit: www.rocketlabusa.com
Described as the world’s first battery-powered rocket, Electron is an entirely carbon-composite vehicle that is 20 metres in length and 1 metre in diameter, with a lift-off mass of 10,500 kg.
Rocket Lab’s CEO Peter Beck said that Electron – capable of delivering payloads of up to 100 kg to a 500 km sun-synchronous orbit – was designed to transform the global space industry with affordable, high-frequency launches of small satellites.
“Historically, the time and expense to launch small satellites have been prohibitive, costing many millions of dollars and requiring endless patience and flexibility waiting for months to ‘hitch a ride’ to space,” Mr Beck said in a press release.
“With Electron, companies can launch whenever they would like, at a substantially more affordable cost. This monumental advancement in space technology gives satellite-reliant businesses the freedom they have been waiting for, which will lead to vast improvements in how we use satellite technology in space.”
Unlike traditional propulsion cycles based on complex and expensive gas generators, the 4,600 lbf Rutherford engine adopts an entirely new electric propulsion cycle, making use of high-performance brushless DC electric motors and lithium-polymer batteries to drive its turbopumps.
Rutherford, named after New Zealand-born physicist Ernest Rutherford, is also the first oxygen/hydrocarbon engine to use 3D printing for all primary components including its engine chamber, injector, pumps and main propellant valves.
“Using this process, Rocket Lab’s engineers have created complex, yet lightweight, structures previously unattainable through traditional techniques, reducing the build time from months to days and increasing affordability,” reads the press release.
Electron’s upper stage is designed with the capability to disconnect the payload integration from the main booster assembly. Sealed integrated payloads can then be transported back to Rocket Lab where integration with the main booster can occur in a matter of hours, which eliminates the risk of cascading delays and allows customers to regain control of the integration process, using their own preferred facilities and personnel.
“Although the privatisation of the space industry has promised an easier path to commercial launches, space has remained an incredibly difficult and expensive place to reach,” Mr Beck said.
“Electron makes it possible for us to continue to execute on our vision to enable easier access to space. As more small satellite companies are able to quickly reach orbit, we will see immense advancements in communication and imaging technologies, which has the potential to drastically change our world – from improved traffic reporting to crop planning to even mitigating the life-threatening damages of natural disasters.”