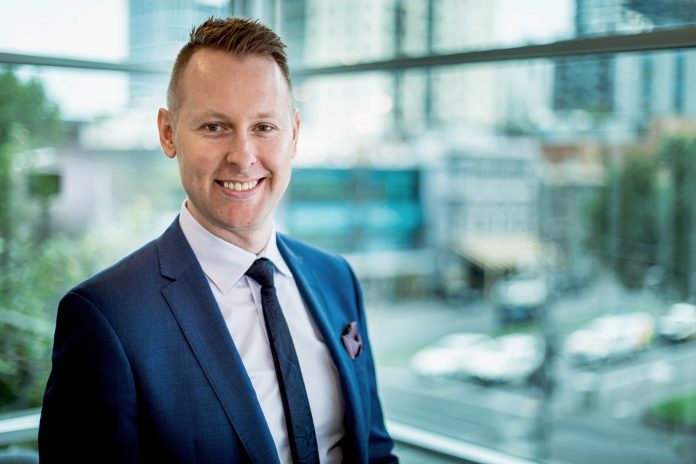
Article by Sam Deckert, Founder and Principal Consultant at Peak Insight Of all the factors that determine success in the manufacturing sector, one of the most important is effective business collaboration. Firms must be in constant contact with everyone from suppliers to distribution partners and end customers. Any failure to collaborate can result in misunderstandings,…