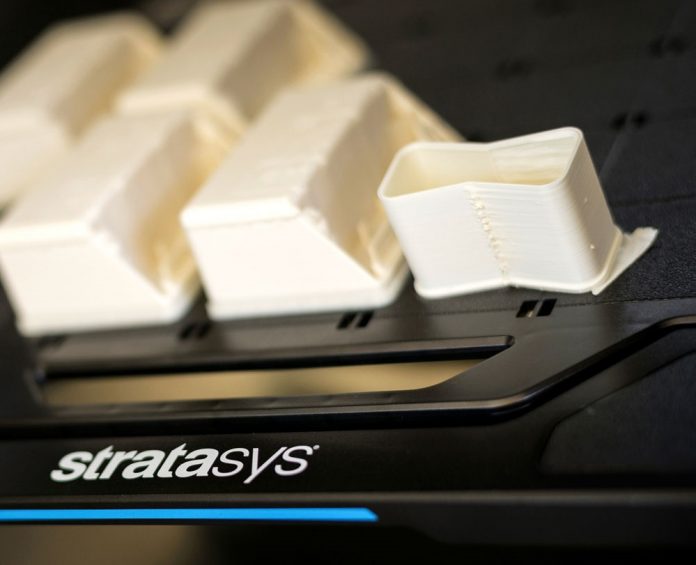
Labour costs have begun to rise making automation more attractive and threatening job security. Focus has also shifted from mass produced products to customised products particularly in the field of consumer products. Fortunately, 3D printing is able to mitigate these changes and allow manufacturing to shift from traditional to advanced production.