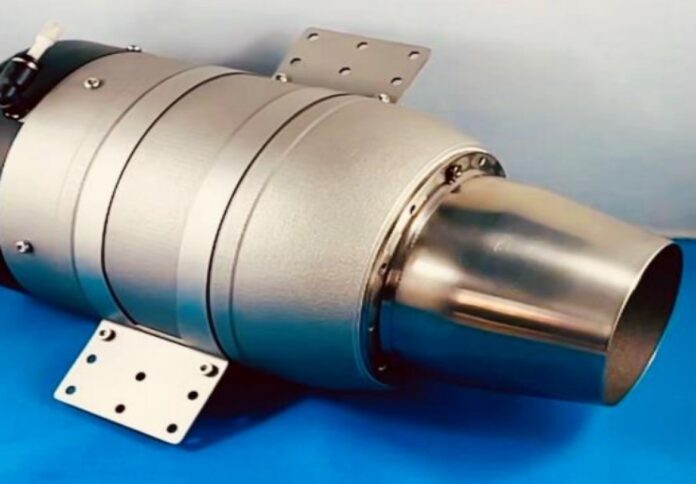
Aurora Labs has manufactured a 200N Class gas turbine engine featuring 3D metal printed parts, marking an advancement in propulsion technology, particularly for applications such as unmanned aerial vehicles (UAVs) and instant power generation systems.
The newly developed micro gas turbine engine, at the heart of a compact propulsion system or power plant, offers the capability to efficiently convert natural gas or liquid fuels into mechanical energy.
Scheduled for market release as early as next month, the turbine boasts lightweight propulsion capabilities tailored to a diverse range of markets, the company said in an ASX announcement.
Simultaneously, efforts are underway to advance the development of a 400N Class model to further expand market opportunities.
CEO Rebekah Letheby underscored the role of 3D metal printing in expediting the product prototyping process for A3D’s sovereign turbine engine.
Within four months, the company had achieved a feat by manufacturing an advanced product, the CEO noted.
In particular, the turbine engine’s design and printing have not only met but surpassed benchmarks for laboratory prototype testing, positioning A3D at the forefront of high-energy 3D metal printing of components.
The next phase of testing involves field deployment, where the engine will be integrated into a remotely piloted airframe.
Letheby expressed confidence in the substantial interest garnered for A3D’s printed engines, which hold promise not only for UAVs but also for instant power generation.
“We have an excellent level of interest for A3D’s printed engines which also have application not only to unmanned aerial vehicles, but also instant power generation,” she explained.
“It is our goal to have a cutting-edge piece of technology to sell to the sizeable defence and aerospace markets.”
In the development of the prototype turbine engine, A3D said it pursued market-established benchmarks for its 200N Class turbine engine.
Essential parameters such as thrust, air intake efficiencies, engine weight, and fuel consumption have been successfully met, with room for further enhancement through unique generative design changes tailored for 3D printing.
Despite comparisons in function and performance with engines built using traditional manufacturing methods, A3D said the engine stands out for its streamlined assembly process, owing to fewer complex parts, without compromising on performance.
Efficiency and weight reduction remain focal points of A3D’s testing initiatives. By strategically selecting lightweight materials and amalgamating multiple parts into single assemblies through 3D printing, significant advancements have been achieved.
For instance, the consolidation of 18 parts into a single printed part has resulted in a remarkable 20 per cent reduction in weight compared to traditional engines of the same class.
Moreover, testing has validated the mechanical strength and metallurgical integrity of the selected metal materials for 3D-printed parts.
These materials exhibit resilience against stress and high temperatures, ensuring reliability and repeatability comparable to conventional metal materials, the company noted.
The versatility of the turbine is further emphasised by its ability to operate on various fuel types, including Jet-A1, kerosene, and diesel fuels, catering to diverse operational environments where specific fuel types may be limited.
In engaging with the defence and aerospace industries, A3D has showcased the current version of its printed gas turbine engine, catering to prospective customers with diverse application requirements.
The company’s commitment to delivering sovereign-designed, manufactured, and assembled engines aligns seamlessly with Australia’s defence capabilities objectives outlined in the Australian Defence Review, 2023.
Looking ahead, A3D said it is poised to capitalise on the market momentum by fast-tracking the design and production of the larger 400N Class gas turbine model.