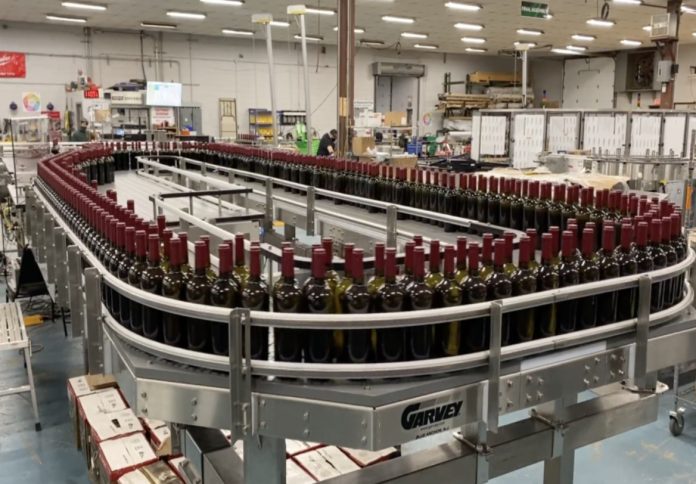
Garvey, a specialist in conveyor and accumulation systems and part of Columbus McKinnon, has turned to advanced visualisation technology to better communicate the value of its bottling line solutions to customers across the food, beverage, pharmaceutical, and household goods sectors.
Seeking a more compelling way to showcase the throughput and efficiency advantages of its accumulation tables, Garvey adopted Emulate3D, a digital twin and 3D visualisation software developed by Rockwell Automation, as revealed in a news release.
Accumulation tables act as buffer zones in manufacturing lines, allowing production to continue smoothly even when temporary stoppages occur in certain stages of filling, labelling, or packaging.
Garvey’s interest in Emulate3D was sparked through internal collaboration with parent company Columbus McKinnon, which had previously worked with Australian firm Glenvern Group – a long-standing Rockwell Automation Partner – on manufacturing visualisation projects.
The group’s Emulate3D application team customised the software for another Columbus McKinnon brand, Dorner, prompting Garvey to explore its potential for their own operations.
“We could see that using 3D visualisation software that kept track of key data points and simulated real-world conditions could better showcase the benefits of our accumulation systems,” said Bill Reese, senior director of engineering at Garvey.
According to Reese, the ability to run simulations on standard hardware and demonstrate real-time input changes during live customer meetings has been a significant asset for the sales team.
“It’s one thing to show a simulation that’s been created in advance, but being able to change inputs and show different scenarios in real time has been a game changer,” he said.
Emulate3D allows users to create high-fidelity, physics-based models of manufacturing and material handling systems.
Glenvern Group director Alec Poulton noted that their team developed a full visualisation of a bottling plant for Garvey, enabling the company to demonstrate how accumulation systems help avoid production downtime and optimise preventive maintenance schedules.
“Essentially, without an accumulation table, if one part of production stops, it all stops,” said Poulton. “With accumulation tables, you have an amount of buffer where production can continue in parts while issues are fixed.”
Garvey leveraged screen-recorded demos and live simulations to present side-by-side comparisons of production scenarios, including detailed metrics such as bottles and cases packed per minute. Reese said this data-driven approach has proven effective in supporting new customer acquisition.
“Rockwell’s Emulate3D software is a game changer for us, and Glenvern Group is highly experienced in how to make the most of it,” he said.
“We’ve enjoyed the collaboration and found Glenvern to be highly responsive with excellent communication throughout the project.”
Columbus McKinnon has since expanded the use of Emulate3D across multiple brands and locations, supported by Glenvern Group’s training, customisation, and technical services.