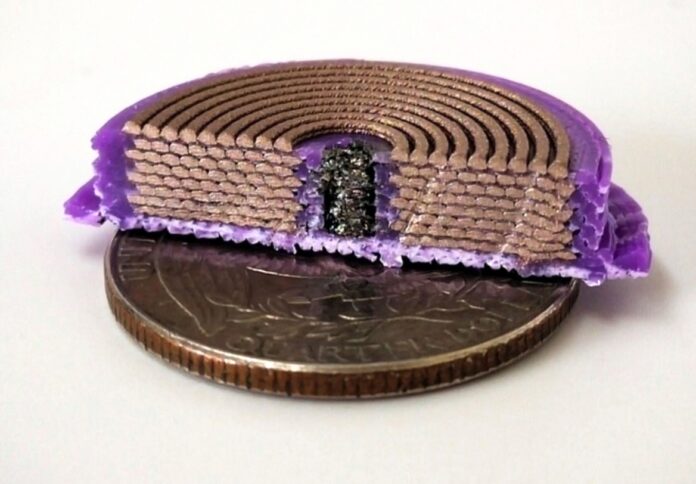
MIT engineers have achieved a groundbreaking feat by 3D printing the core components of electromagnets, marking a significant leap forward in the realm of electronics manufacturing.
In a news release, the research team said it envisions a future where entire medical devices, such as dialysis machines, can be constructed solely using 3D printers.
This innovative approach not only aims for cost reduction and elimination of manufacturing waste but also holds the potential to facilitate easier access to vital medical equipment for individuals in remote areas or with limited resources.
While overcoming multiple obstacles is necessary to fully realise the concept of entirely 3D-printed electronic devices, MIT researchers have demonstrated fully 3D-printed, three-dimensional solenoids.
Solenoids, electromagnets formed by a coil of wire wrapped around a magnetic core, serve as fundamental building blocks in various electronic devices, ranging from dialysis machines and respirators to household appliances like washing machines and dishwashers.
The team achieved this milestone by modifying a multimaterial 3D printer to enable the seamless printing of compact, magnetic-cored solenoids in a single step.
Researchers said this innovative approach eliminates defects that could arise during post-assembly processes.
Utilising a customised printer capable of using higher-performing materials than conventional commercial printers, the researchers produced solenoids capable of withstanding twice as much electric current and generating a magnetic field three times larger than other 3D-printed devices.
Luis Fernando Velásquez-García, a principal research scientist in MIT’s Microsystems Technology Laboratories (MTL) and the senior author of the research paper published in the journal Virtual and Physical Prototyping, highlighted the transformative potential of this technology.
He emphasised that additive manufacturing can democratise access to advanced technologies by enabling local production rather than relying on centralised manufacturing centres.
The modified printer utilises a process called extrusion printing, which fabricates objects layer by layer by extruding material through a nozzle.
By precisely layering three different materials—a dielectric material serving as an insulator, a conductive material forming the electric coil, and a soft magnetic material comprising the core—the team successfully printed solenoids with enhanced performance.
Despite the challenges posed by the use of multiple materials, including the need to prevent cross-contamination, the researchers retrofitted the printer to extrude pellets instead of filament, allowing for the printing of soft magnetic nylon—a material crucial for optimal solenoid performance.
While the customised hardware incurred a cost of approximately $4,000, Velásquez-García noted that this technique remains more cost-effective than alternative approaches.
The precision and versatility of the modified printer enabled the production of compact solenoids with improved performance compared to conventional 3D-printed devices.
Moving forward, the researchers aim to further enhance performance by exploring alternative materials and refining the printing process to reduce defects.
This research was funded by Empiriko Corporation.