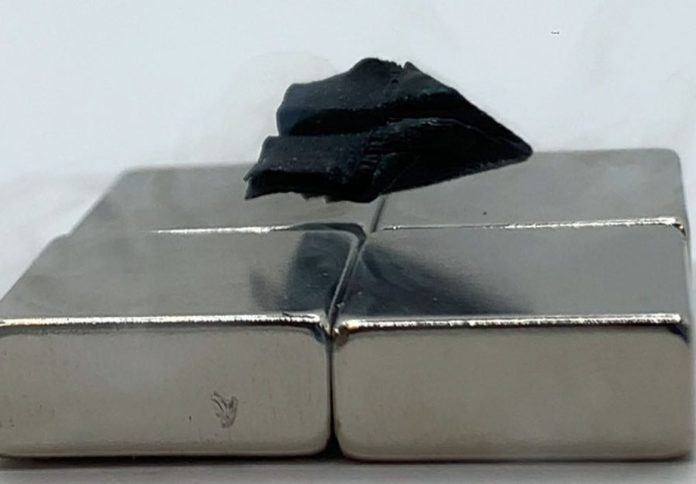
Researchers at Northwestern University, with support from the US Department of Energy’s Fermi National Accelerator Laboratory (Fermilab), have developed a groundbreaking method for 3D printing high-temperature superconductors.
The technique, detailed in Nature Communications, marks the first time ceramic superconductors have been 3D printed with a monocrystalline microstructure, as stated in a news release.
Superconductors are materials that can carry electricity without resistance, but only at extremely low temperatures.
High-temperature superconductors, which operate at comparatively higher (yet still very cold) temperatures, are more practical for many technologies.
These materials are used in power generation, MRI machines, and magnetically levitated trains. They are also essential in particle accelerator technology due to their efficiency in high magnetic fields.
The new method was supported through Fermilab’s Laboratory Directed Research and Development (LDRD) program. Cristian Boffo, project director for Fermilab’s Proton Improvement Plan-II, helped secure the funding.
The research aligns with Fermilab’s broader goal of developing advanced superconducting magnets and components.
“Fermilab wants to make better and better magnet systems that are more efficient and reach higher performance,” Boffo said.
“Northwestern provides the experience in 3D printing, and we provide experience in superconductors.”
The process begins with 3D printing a ceramic superconductor using a common powder called yttrium barium copper oxide (YBCO). After sintering, or baking, a single-crystal seed made of neodymium barium copper oxide (NdBCO) is placed on the printed structure.
The structure is then partially melted and slowly cooled in a process called top seeded melt growth. This allows the printed part to adopt the single-crystal orientation of the seed, resulting in a monocrystalline structure while maintaining the complex 3D shape.
“This new technology will enable new magnet designs, leading to higher performances and potentially even allow the production of a new generation of superconducting radio-frequency cavities,” Boffo said.
Northwestern professor David Dunand, who co-authored the study with his graduate student Dingchang Zhang, said the method could be scaled up and used in many settings.
The team has already created parts up to 10 centimeters in diameter and even shaped a foil into a miniature paper airplane to demonstrate the material’s flexibility.
“If we want to use it for accelerators, we need to print larger parts,” Zhang said, adding that their next steps include exploring multi-seed approaches to scale up the technology.
The development offers potential applications in both scientific research and practical technologies, with the added advantage of reduced cooling costs through the use of liquid nitrogen instead of liquid helium.
Fermilab is the US Department of Energy’s premier laboratory for particle physics and accelerator research.