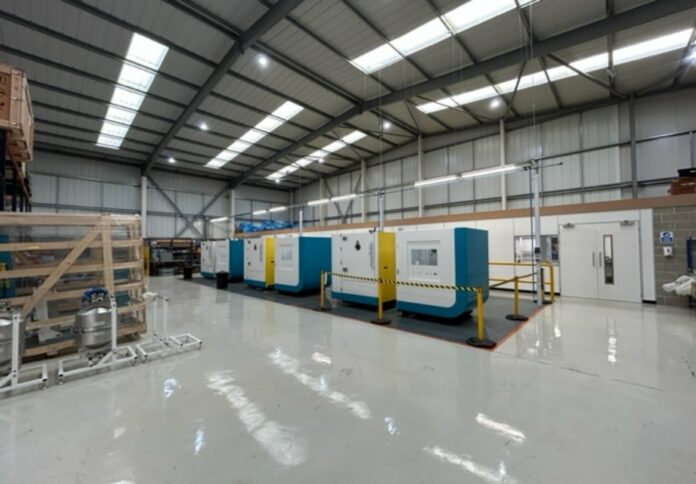
Wayland Additive said it is ramping up the production of its Calibur3 metal Additive Manufacturing machine in a push to “insulate customers against supply chain delays.”
In a press release, Wayland said it currently has six machines producing goods to fill orders.
The company also provided some details on the initiatives it is launching to overcome and address the various supply chain issues that have plagued the international industry in the aftermath of the pandemic.
In an effort to shorten delivery periods, the company is shifting away from its previous ‘make to order’ strategy and toward one in which consumers can purchase the Calibur3 “off-the-shelf” by producing an additional ten machines by the end of 2023 and 24 more in 2024.
Dan Rushton, operations manager at Wayland, stated, “We have, over the last few months, doubled the size of our production facility, have added an inspection and workshop area, have installed an impressively large carrousel where all machine parts are sorted & stored, and, working towards 2025, will boast a new applications centre and an R&D centre, as well.”
In terms of supply chain issues, Rushton said the company has invested time and resources into extending the supply chains into new regions and developing relationships on a worldwide scale, which has allowed Wayland to access a far wider network of possible suppliers.
“We are also securing future stock through pre-orders and strong supplier relationships, which is only possible with a level of financial robustness that can carry the burden,” he added.
To date, Wayland’s Calibur3 delivers all of the benefits of metal electron beam (eBeam) powder bed fusion (PBF) technology while resolving the problematic problems that have historically prevented widespread implementation, the company said.
Wayland also emphasised that the technology produces fully dense parts in highly reflective alloys and refractory metals like tungsten, free of residual stresses, and with less energy consumption.
The company claims the solution opens up a range of applications across various industry sectors that were previously unable to benefit from the use of 3D printing as a production process.