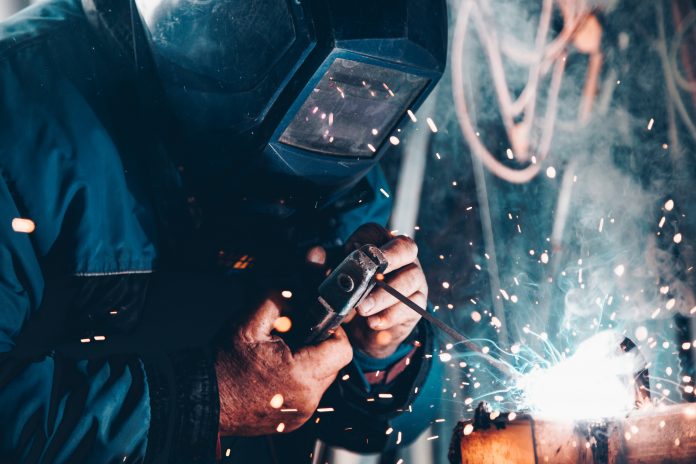
Article by Stephen Moore, Managing Director, Asia Pacific Japan at Ceridian This past year highlighted the importance of every organisation’s ability to be agile and embrace change. COVID-19 kickstarted a new chapter for the manufacturing industry in Australia. As borders closed and demand for essential products rose, forward-thinking organisations within the industry looked to shift operations quickly and create a revitalised source…