An Australian plastics manufacturing company has made some of the sets for the new Wolverine movie using a special vacuum forming process.
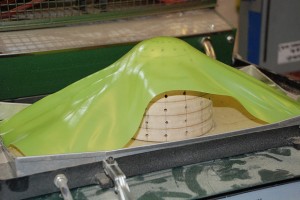
Image credit: Flickr user JordanHill School D&T Dept
According to the company’s blog, Sydney-based BR Plastics was able to create much of the internal train used in the Hugh Jackman movie by employing their special large sheet vacuum forming process which they have also used for set components in other well-known movies.
“Vacuum Forming is a well developed and highly versatile process which gives excellent hard wearing large plastic parts with inexpensive tooling costs,” says BR Plastics.
Vacuum forming process has a number of advantages over other forms of plastic molding. These include lower tooling and set-up costs, shorter lead times, flexible design changes, lower internal stress on the product and reduced weight, among others.
Vacuum forming is actually a simplified version of thermoforming in which a sheet of plastic is heated to a temperature at which it can be formed, either by being stretched onto or into a single-surface mold and held against the mold by applying a vacuum between the mold surface and the sheet.
Using a modern CAD product design system backed by the ISO 9002 quality assurance, BR Plastics can provide large sheet vacuum forming and recommend the most suitable grade of plastic for any purpose. The company can form parts from most common sheet, ABS, Acrylic, PET, HDPE and PP, in sizes up to 4 meters and 10mm thick.
With over 50 years of experience in plastic molding BR Plastics can design and manufacture custom and proprietary products for the Australian and international markets. Their portfolio includes products such as pre-school activity equipment, equestrian equipment, canoes, marine buoys, water tanks and storage bins and drums.