Many manufacturing businesses are struggling to meet the ever-growing customer expectations in an increasingly demanding and competitive business environment.
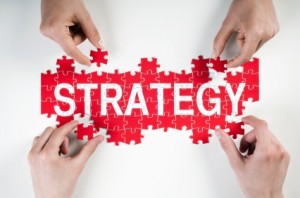
According to SAI Global, there is an inextricable connection between delivering an impressive customer result and the quality of a company’s internal operations.
“It’s surprising that most organisations continue to operate without implementing an effective quality management system, especially when failing to do so can be detrimental to both reputation and profit,” says David Gray, quality management trainer at SAI Global.
“The consequences may include ongoing operational delays, budget overruns, and a waste of precious resources. As a result, both a business’s reputation and profit may be at serious risk.”
Many companies have inadequate management systems and are led by managers that lack any official training or education.
“In some companies quality management can land on the lap of an employee who hasn’t undergone any training whatsoever. While this may have been a natural step within the business structure, it may be detrimental to overall performance,” said Mr Grey.
The importance of having an efficient quality management system managed by a qualified staff member cannot be overstated.
A properly managed company is in a position to constantly improve its performances and internal efficiency, to pin-point any inconsistencies and problems, and address to them accordingly. As a result, staff morale and productivity is increased and consumers are given confidence in business.
SAI Global offers 6 foolproof steps to instill quality processes in your business:
- Document your model. Make sure you have a person responsible for quality management, one that will ensure that the company has a policy in place that defines its “quality promise”, underpinned with stated objectives and targets for employees. It’s is also essential that you include a defined “roadmap” to guide employees to fulfilling that promise.
- Know your competitors and gain a clear understanding of your difference in the marketplace. Get to know your customers too, and learn what they value most about your products and services. Build healthy relationships with employees and communicate this information to them.
- Provide your employees with clear guidelines as to their responsibilities within the company’s structure. Engage employees by delegating responsibility and authority to deliver the promise of quality made by the organization to its customers.
- Deliver on your promises of quality, not forgetting the aspects that are outsourced to external third-party providers. Do they understand what your promise of quality is and their role in keeping this promise?
- Constantly monitor and measure performance results to determine if the promise of quality was delivered. This will allow you to assess whether the required quality was delivered and provide you with baselines to gauge success.
- Implement the knowledge. Remove these obstacles through controlled changes in your operations. If you have a quality plan in place you will be able to assess which process is most appropriate to the issue and apply the solution in a timely manner to achieve results.