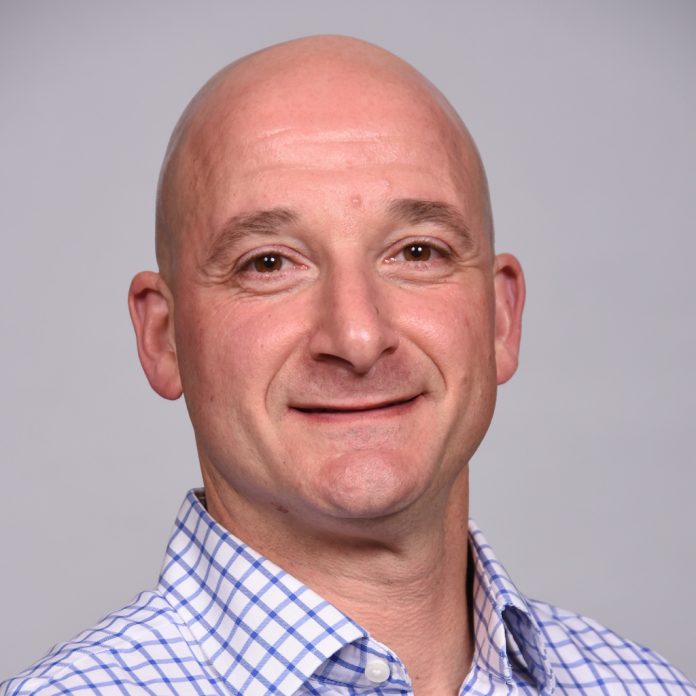
This article is by Gideon Joseph, Manufacturing, Services and Distribution Practice Manager at Kronos Australia has historically been a manufacturing powerhouse. In fact, by the 1950s more than a quarter (28%) of all employed Australians were working in the industry. However, by the 1990s offshoring had become incredibly popular, with companies looking to Asia to…