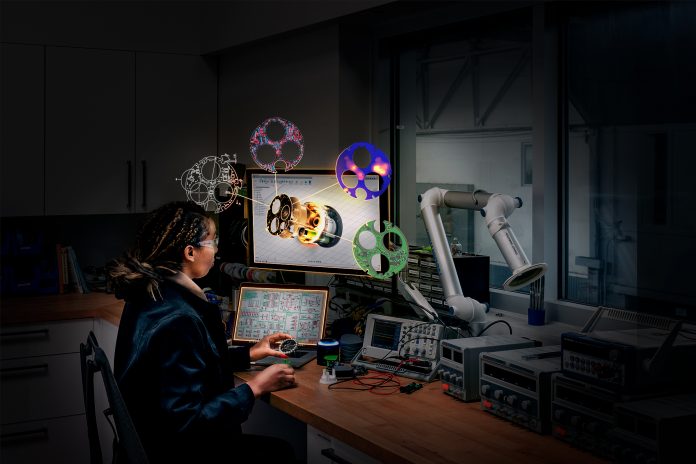
In today’s cloud-connected world you would expect design tools to have overcome the collaboration challenges facing electronics and mechanical designers. Yet, most development teams still struggle relying on manual methods, such as emails and exchanging files, to overcome such a complex task.