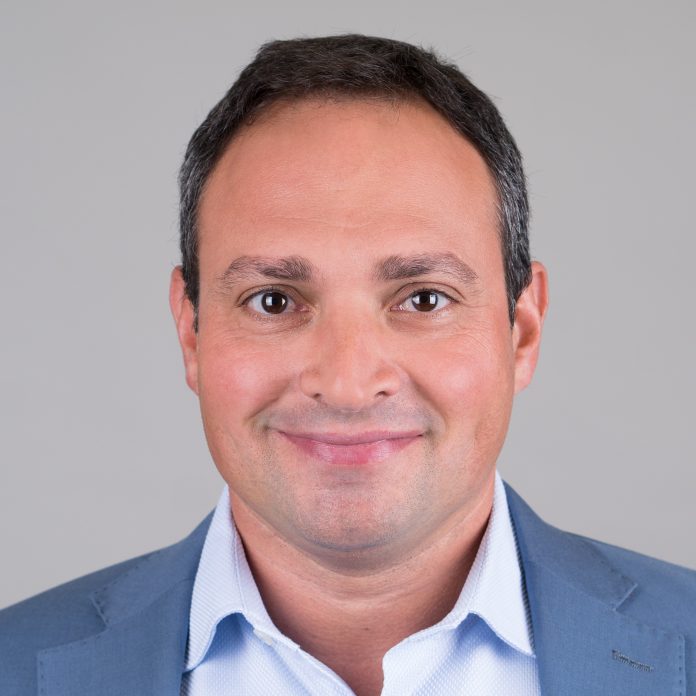
Manufacturing businesses have a strong incentive to improve their financial bottom line and return on investment, cut labour costs and increase productivity. To do this, organisations need to not only invest in IIoT technology, but they also require software to manage and monitor their networks.