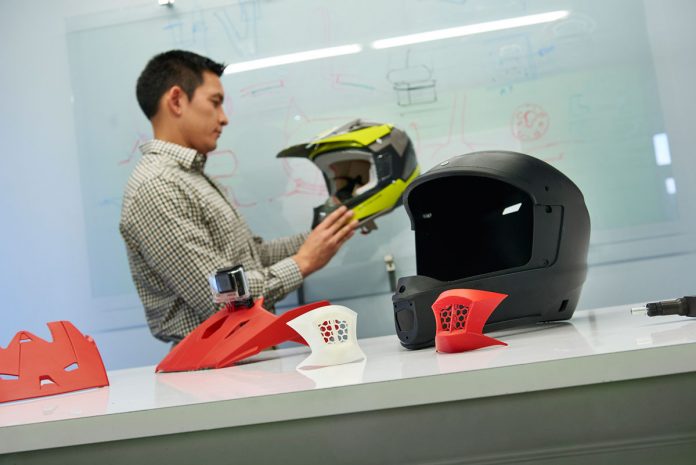
In 2011, an article in the Economist noted that 3D printing “makes it as cheap to create single items as it is to produce thousands”. This simple yet profound description best describes the disruptive potential of 3D printing and why everyone is clamouring to jump on the 3D printing bandwagon.