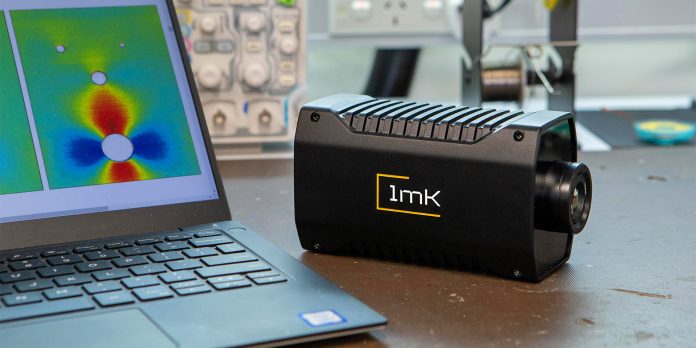
Article by Kheang Khauv, Managing Director of 1MilliKelvin
The LTS-640V is a digital imaging machine little bigger than a DSLR camera that provides real time imagery that helps quantify material stress and detect fatigue cracks that could prove dangerous if unchecked.
The LTS-640V is designed to be used during the certification stage before an aircraft is approved for commercial or military use. The capability it provides will allow for a potentially more streamlined certification process, and should help eliminate some of the surprises that can occur during testing of a new aircraft structure.
The technology was developed in collaboration with scientists at the Australian Department of Defence where a prototype of this technology has helped support sustainment of the F/A-18 Classic Hornet, and more recently provided Lockheed Martin Aeronautics with valuable new information during structural certification testing of the F-35 Joint Strike Fighter.
The Australian invention is the first of its kind, providing real time fusion of stress and visible spectrum imaging – in effect merging the visible with the invisible.
‘This inspection approach is based on the ‘thermoelastic effect’; put simply, when you squash something it heats up, when you stretch something it cools down’, says a spokesperson for Defence. ‘Think of magic spray which is often used to treat sports injuries – it’s the stretching or expansion of the gas as it leaves the aerosol can that provides the cooling effect.’
‘Unlike magic spray however, the temperature changes we’re dealing with are tiny, thousandths of a degree, but we can still detect them, and quite easily using the advanced algorithms at the core of this technology’.
This capability has a significant role to play in helping aircraft designers and operators better understand how an airframe performs under load. ‘The technology can improve our ability to quantify stresses, particularly in structurally critical areas where traditional technologies have very limited capability’ says a Defence spokesperson.
‘We are looking to help streamline and improve structural validation processes across the global defence and aeronautics industries’, says Mr Kheang Khauv of 1MILLIKELVIN.
‘This technology has been used to support the Classic Hornet and has demonstrated in the F-35 full scale durability test program how it can improve the way designers validate modelling of complex airframe components.’
‘We are proud our advanced technology is making a contribution to Defence capability’.
And the applications of this extend well beyond aviation, with potential customers including industry both at home here in Australia and around the world.
With $275,000 of grant funding, the design team at 1MILLIKELVIN have transformed this groundbreaking capability into a robust commercial product. Total grants so far are $75,000 from VIC government (Boost your business program), $150,000 from the Advanced Manufacturing Growth Centre and another $50,000 from the Defence Science Institute Defence Science Institute – Defence Science Institute, which is part of the Australian Defence Science and Universities Network Australian Defence Science and Universities Network (ADSUN) | DST