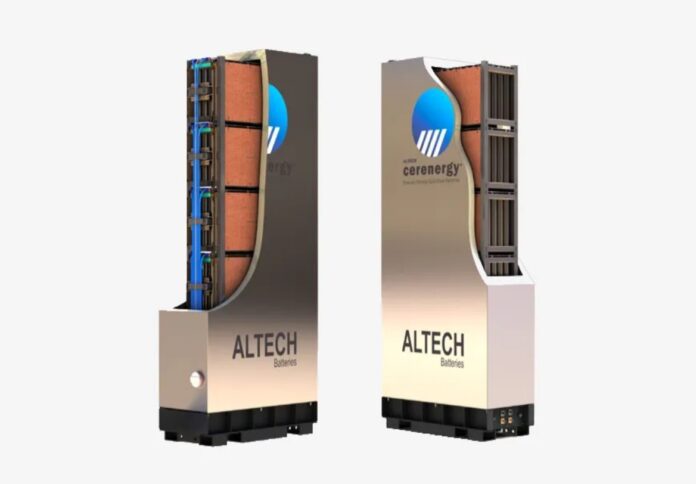
Altech Batteries announced that it has finalised the design of its 60KWh battery pack after extensive collaborations with component suppliers.
The ASX-listed company said the design has undergone significant improvements, now featuring a sleek stainless-steel exterior with the prominent CERENERGY logo on top and “ALTECH Batteries” engraved at the bottom.
One of the primary enhancements is the adoption of a stainless-steel casing that replaces the previous blue paint.
This new casing is designed to withstand extreme temperature variations, from snowy to desert conditions, all while maintaining its pristine appearance.
To ensure optimal insulation, the battery’s casing is equipped with a vacuum-sealed, double-sided enclosure.
Given the internal temperature of approximately 270 degrees Celsius, minimising heat transfer losses and ensuring human safety is of utmost importance.
The base of the battery has also been reinforced to accommodate high-temperature-resistant electrical cables and connectors, further reducing heat loss to the environment.
To address cold-starting issues, heating pads have been integrated into the vacuum-packed casing. The heating process typically takes around ten hours before the battery is fully activated.
Once initialised, the battery efficiently maintains its internal temperature with minimal reliance on the heating pads.
Additionally, improvements have been made to the internal frames, each housing 48 cells, to optimise their performance.
The connector plates, responsible for electrically linking the cells while maintaining insulation with mica insulation, have been meticulously designed. The cells themselves are connected through precise laser-targeted welding.
As previously announced, two working prototype ABS60 KWh batteries have been ordered from Fraunhofer Institute partners.
The production of these packs is already underway, with about half of the required cells already completed. While the production capacity is limited by the size of pilot plant equipment and kiln capacity at the Fraunhofer Institute, significant progress has been made.
Simultaneously, the first stainless-steel vacuum-sealed battery case has been delivered to the Fraunhofer Institute in Dresden.
Comprehensive heat transfer loss testing and temperature profiling will be conducted on the battery casing before assembling the battery cells. Once the cells are completed, they will be assembled into the pack for further cycling and long-term performance tests.
Group Managing Director Iggy Tan expressed his satisfaction with the battery’s optimisation and the progress of the prototypes.
“The vacuum-sealed casing will provide the perfect insulation and minimise any heat loss, which is the key benefit of our sodium chloride solid-state batteries,” he noted.
Tan continued, “The production of the prototype batteries is progressing well. The produced cells are performing well under bench performance testing and it will be great to see the whole 60KWh unit under performance load. This is the first time our partner Fraunhofer has made such a large battery unit”.