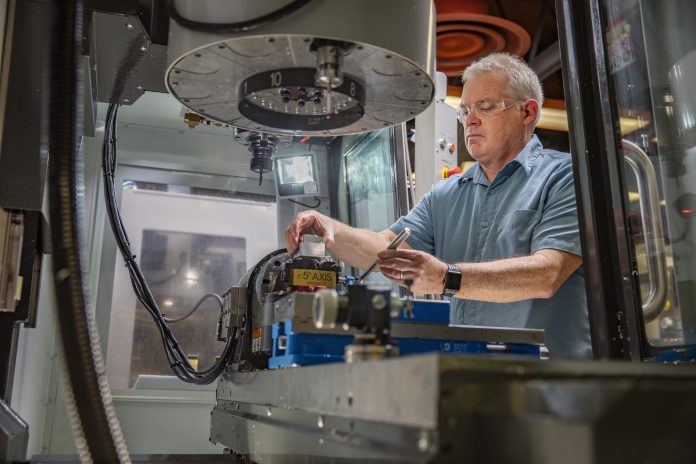
Sponsored Content by
Projects are becoming bigger and bigger with increasingly aggressive deadlines to meet as the modern factory interweaves innovation into its core processes. And with massive progress, we are bound to encounter an equally massive problem that comes with it.
There is no denying that the manufacturing sector has a problem with waste reduction and we do not need an environmental scientist pointing it out in order to realize the issue.
Aside from its devastating effects on the environment, waste production also impacts the supply chain’s resiliency, ultimately affecting our financial stability and product integrity.
In the construction industry, for example, over 3 billion metric tonnes of natural resources are needed to manufacture building materials every year globally. Up to 30 per cent of this is wasted, with rework, overestimating, and inaccurate data all contributing to the problem.
In a study conducted by Autodesk, approximately 52 per cent of the company’s design and manufacturing customers have rolled out sustainable practices. In 2019, Autodesk and IDEO hosted a workshop with designers, manufacturers, and consultants to explore potential process models that could better support sustainable product design and reduce waste production.
System integration and its relevance
No matter the industry, interoperability plays a significant role in keeping everyone posted at every step of the process. By looking at the whole picture and having all the information needed along the way, businesses can provide a better user experience or offer enhanced product integrity.
In manufacturing, it is crucial to determine the quality of products, which also means the reduction of wasted materials. One designer or engineer is not necessarily the right person for each component, particularly as products across various areas of specialty become increasingly more complex.
Getting to the root of the issue
Aside from the massive environmental factor that comes into play in the absence of waste management, time, money, energy, and materials also go down the drain due to poor design and inefficient production cycles.
According to Autodesk’s 2020 Sustainability Report, manufacturers are poised to reduce energy use by up to 25 per cent and boost productivity through the use of smart and connected manufacturing techniques.
In a bid to achieve a responsible and sustainable supply chain, business leaders must grab the opportunity to step up their supplier evaluation to ensure product compliance and enhance the monitoring of failure analysis and reports.
Project predictability can be achieved by taking a step back to look at the bigger picture and tap into the integration of design and manufacturing processes.
Australian Manufacturing, in cooperation with Autodesk, is hosting the “Production Efficiency in Manufacturing” webinar to convene industry leaders and facilitate an exchange of ideas on waste reduction and interoperability best practices.
To register and for more information, please visit Australian Manufacturing’s event page.