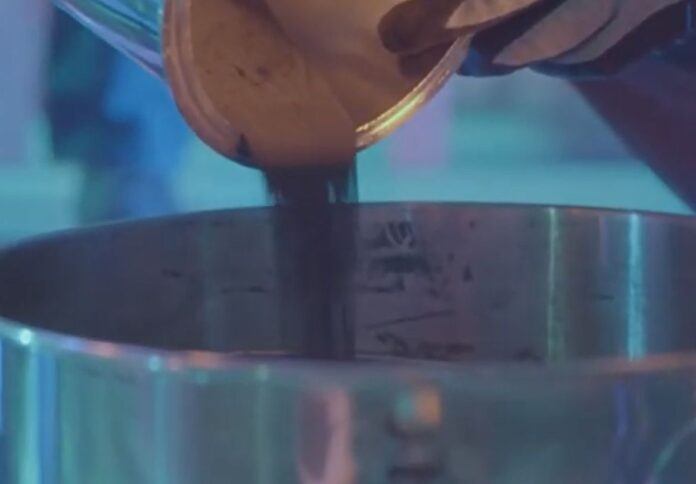
IperionX has won the prestigious R&D 100 award for its innovative Hydrogen Assisted Metallothermic Reduction (HAMR) technology – a low-cost and sustainable process for producing high-value titanium metal powder.
In many applications, titanium outperforms steel and aluminium, but its high cost has generally limited its use to high-performance applications, IperionX said in an ASX announcement.
IperionX and the technology’s maker, Dr Zak Fang, have received recognition for HAMR, which can be used for creating titanium metal powder that can be utilised in both additive manufacturing and conventional powder metallurgy processes.
Using either 100 per cent recycled titanium scrap or titanium minerals, the proprietary HAMR technique can create titanium metal, the company revealed.
The resulting high-quality titanium powder can be utilised in powder metallurgy or additive manufacturing to create items for a variety of demanding industries, such as aerospace, defence, and biomedicine, at significantly lower costs.
The R&D 100 Awards are the only global science and technology awards program that honours new commercial products, technologies, and materials for their technological relevance.
The awards are also recognised as a mark of excellence for the most inventive ideas of the year in industry, government, and academia.
IperionX CEO Anastasios Arima expressed his gratitude to Dr Zak Fang, his team at the University of Utah, and the company for developing and commercialising the HAMR technology to generate low-cost, sustainable titanium metal powders.
Arima emphasised the significance of its commitment to innovation as well as the substantial progress made in developing and commercialising this distinctive titanium technology.
For more than 50 years, IperionX said much effort has been invested in developing a new technology to replace the current Kroll method in order to reduce the cost and environmental effect of titanium metal production.
To date, these initiatives have failed to achieve quality standards, cost-cutting requirements, or commercial scalability.
Unlike the Kroll method, the HAMR process uses low-temperature processing, which decreases direct carbon emissions and significantly lowers the cost of creating titanium metal.
The HAMR process, when fed 100 per cent titanium scrap, can create a circular supply chain for this advanced metal, which is crucial to America’s economic future and national security.
“Commercialisation of the HAMR process has been successfully proven, with high-quality titanium powder currently being produced at IperionX’s Industrial Pilot Facility in Salt Lake City, UT,” IperionX said in a statement.
IperionX has advanced plans to establish a larger titanium production facility in Halifax County, Virginia, to address the increasing need for sustainable and lower-cost titanium metal.
Once operational, IperionX said it intends to rapidly grow the capacity of this unique titanium production facility in a low-risk, modular manner.