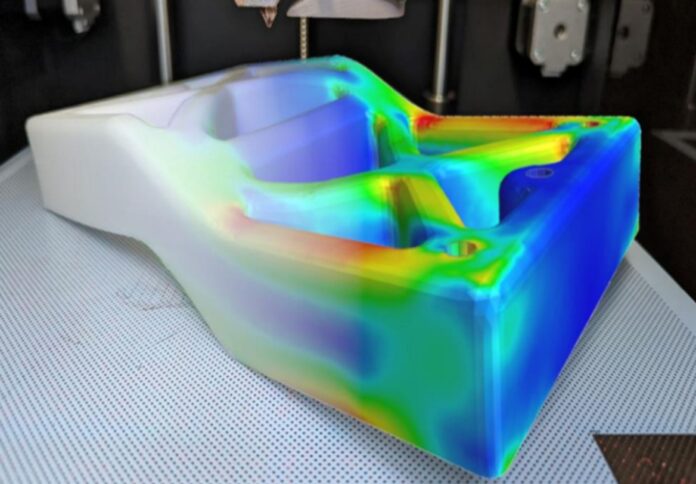
A two-year Innovate UK-funded initiative known as OverHiPP, focusing on Over-printing with High Performance Polymers, sees GRM, a TriMech Group entity, collaborating with five other project partners and a varied advisory board.
The primary objective of OverHiPP is to pioneer and refine a novel hybrid manufacturing technique, blending the capabilities of overprinting 3D materials onto composite sheets, GRM Consulting said in a media release.
This innovative approach unites the strengths of existing methodologies such as over-moulding, resin transfer moulding (RTM), and 3D printing, promising reduced tooling costs, enhanced flexibility, swift material changeover, and minimized material wastage.
However, despite its potential, the venture encounters challenges owing to limited knowledge and technological constraints.
Recent strides in five-axis 3D printing hardware have expanded the horizons of technological possibilities. By diminishing the necessity for support structures, these advancements enable the creation of shapes hitherto deemed unattainable, even with conventional 3D printing methods.
Notably, the capability to over-print material onto existing components marks a significant milestone in additive manufacturing.
Nonetheless, the pace of development in simulation techniques for such intricate 3D printed structures lags behind, presenting a critical bottleneck.
Addressing this gap, GRM Consulting, renowned for its expertise in design and topology optimization software, has been pivotal in developing cutting-edge solutions.
Leveraging extensive experience in Finite Element Analysis (FEA), GRM has devised innovative software tailored for the OverHiPP project.
This software aims to augment the accuracy of digital twins, offering invaluable insights, guidance, and confidence in the structural integrity of 3D printed components.
The inherently anisotropic nature of 5-axis 3D printed structures poses a challenge in accurately modelling their properties into digital twins, hindering comprehensive understanding of structural performance and failure modes.
GRM’s solution entails the development of software capable of automatically replicating toolpaths in an FE model.
Utilizing a proprietary G-Code reader, this software analyzes and discerns toolpath properties before translating them into digital twin format, ensuring precise filament orientations and infill cavities are considered during structural simulations.
Rigorous testing conducted by GRM has showcased promising results. A notable experiment focused on the feasibility of 3D printing a hyper-car footrest, involving extensive topology optimization studies to delineate key load paths and structural performance.
The ensuing CAD model, synthesized from the topology results, was prepared for manufacture at the Centre for Additive Layer Manufacturing (CALM) at Exeter University, utilizing high-temperature polyamide from Lehvoss.
Subsequent tests revealed a five-fold difference in both stiffness and strength performance between prints in poor and optimal directions.