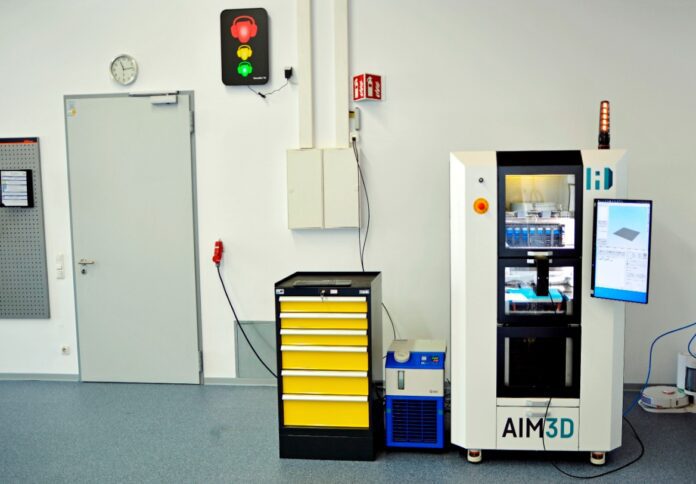
Multi-material 3D printing company AIM3D announced that the Naddcon research and development centre in Lichtenfels, Germany, which specialises in additive manufacturing, has integrated its ExAM 255 3D printer into a Siemens NX package.
The goal of AIM3D was to integrate a “classic” industrial design tool into the process chain, according to a press release by the company.
Siemens NX includes CAD, CAM, and CAE solutions, and Naddcon integrated the ExAM 255 into the NX environment to provide access to the 3D CEM system as a digital machining system.
According to AIM3D, the NX integration is one of “many” options in the open machine concept of AIM3D’s multi-material 3D printers.
Users can also utilise a different method to operate 3D printers and generate G-code, which is a programming language that is used to program numerically controlled machine tools.
AIM3D further explained that it is made up of path conditions (G-words) and additional functions (M-words), each of which is assigned a movement or an action.
Moreover, the 3D printer is integrated as a CAM processing device through the bridge between the machine firmware of AIM3D and the CAD/CAM environment of Siemens NX.
A 3D component’s bionics, free-form surfaces, selectable densities (varying filling techniques), and weight reductions like grid structures can all be optimised based on a desired requirement profile, AIM3D said.
The 3D printing company further claims that a database system and potent simulation models are available.
According to the AIM3D, the entire 3D printing process from design to production can be better regulated, components can be designed optimally, and great reproducibility can be attained at the same time.
Naddcon’s Sebastian Kallenberg designed the integration steps based on a standardised component made of PA6 GF30, the design of which was to be optimised using NX.
On the ExAM 255, the programming was tested on a sample component made of PA6 GF30, the demonstrator.
The tool path was generated first, and then tests on the machine were performed to identify the optimal process parameters, as well as possible errors in the post-processor.
“Our digital NX approach is intended to better exploit the CEM machine technology of AIM3D from a design point of view. There is considerable potential here for free-form surfaces, that is, real 3D contours, but also bionic design strategies,” said Kallenberg.
The outcomes demonstrated that several optimisations may be applied to the demonstrator using NX, according to the company.
Users can also adjust densities, incorporate lattice structures to minimise weight, regulate shrinkage, add stiffeners, and relocate drill holes to best design the entire component and print it using a 3D printer in a professional manner.