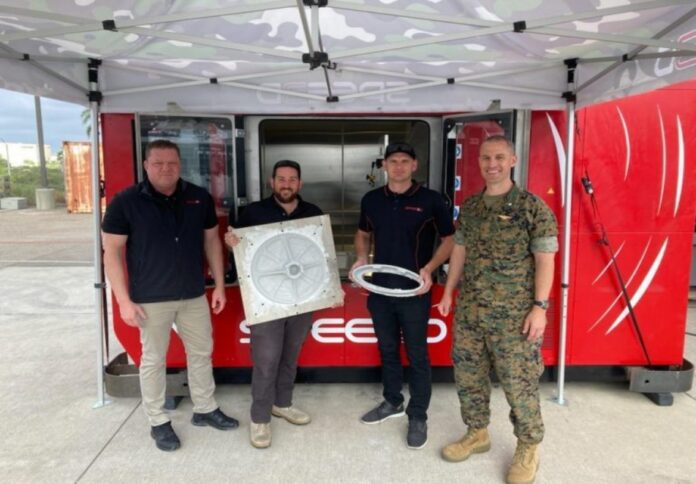
Victoria-based additive manufacturing company SPEE3D has successfully participated in the annual US Marine Corps Integrated Training Exercise 4-23 (ITX), printing on-demand parts in the field to support crucial defence operations.
The event is a live-fire exercise that will train battalion and squadron-sized forces in the tactical application of combined-arms manoeuvre and offensive and defensive operations during conflict, SPEE3D said in a press release.
Over the course of a month, ITX evaluated the skills and adaptability of a force of more than 3,700 Marines and sailors through a series of incremental exercises.
WarpSPEE3D from SPEE3D was sent to the live fire Marine Corps Air Ground Combat Centre Twentynine Palms, California, to print vital components that had been damaged while being transported from ground support at the Marine Corps Air Station in Miramar, California.
Throughout the past few years, SPEE3D has regularly demonstrated its expeditionary point-of-need defence capabilities by participating in numerous military field trials with the US, UK, and Australian armed forces.
Chris Harris, America’s Vice President of Defence for SPEE3D, said it is a privilege to be invited. He is also looking forward to collaborating with the United States Marine Corps on future training exercises.
“Our involvement in ITX 4-23 is yet another testament to our commitment to partnering with the military worldwide to provide the best outcomes for rapidly printing 3D metal parts where they are needed the most – near the warfighter,” Harris stated.
Meanwhile, Chris Curran, program manager for the Consortium for Additive Manufacturing Research and Education (CAMRE), explained, “For two consecutive weeks during Integrated Training Exercise 4-23 with the U.S. Marine Corps Forces Reserve, SPEE3D repeatedly demonstrated their ability to 3D print metal replacement parts, outdoors, in an expeditionary environment.”
According to him, what was significant was their capacity to make parts in hours rather than days, which may potentially provide a competitive advantage to warfighters and maintainers in a disputed situation.
SPEE3D said WarpSPEE3D is the world’s first large-format metal 3D printer to use SPEE3D’s patented Cold Spray Additive Manufacturing (CSAM) technology, allowing for quick, cost-effective, and scalable production.
Furthermore, XSPEE3D, developed just last year and specially designed for military use, is an easily transportable 20ft shipping container unit that holds the printer and accompanying equipment, allowing metal parts to be manufactured.