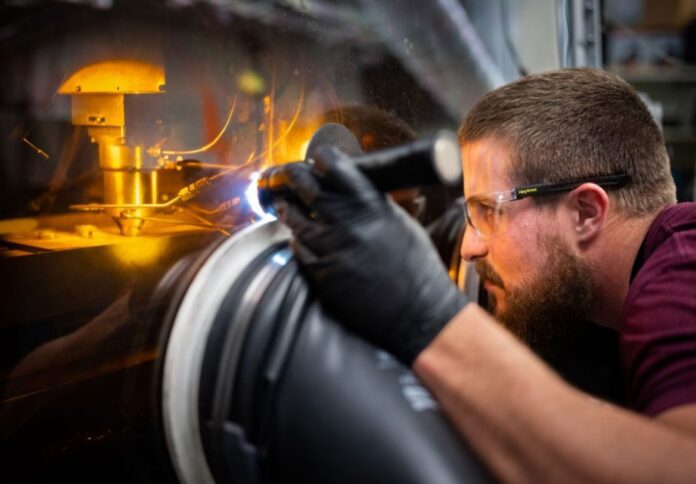
An aspect limiting the production of today’s power hubs is the metals used in the blades, bearings and seals of their steam turbines, which tend to soften and elongate far before their melting point. The challenge goes on as more scientists attempt to lessen its impact on the environment. If these issues are resolved, it is possible to increase the temperature of anything that uses a steam turbine to convert heat into electricity while cutting greenhouse gas emissions.
Researchers at Sandia Labs, Ames National Laboratory, and Iowa State University say they have created a 3D-printable high-performance superalloy with an unusual composition that makes it stronger and lighter than state-of-the-art materials currently used in gas turbine machinery.
The discovery, whose results were published in the journal Applied Materials Today, is claimed to have extensive implications for the energy sector as well as the aerospace and automotive industries. It also raises the possibility of a new class of related alloys that are still undiscovered.
High heat resistance material for power plant turbines
According to the U.S. Energy Information Administration, approximately 80 per cent of electricity in the States is generated by fossil fuel or nuclear power plants. Heat is used in both types of facilities to turn turbines that generate electricity, and the temperature of metal turbine parts limits power plant efficiency. If turbines can operate at higher temperatures, “then more energy can be converted to electricity while reducing the amount of waste heat released to the environment,” said Sal Rodriguez, a Sandia nuclear engineer who did not participate in the research.
Sandia’s tests revealed that the new superalloy — 42 per cent aluminium, 25 per cent titanium, 13 per cent niobium, 8 per cent zirconium, 8 per cent molybdenum, and 4 per cent tantalum — was stronger at 800 degrees Celsius (1,472 degrees Fahrenheit) than many other high-performance alloys, including those used in turbine parts today, and even stronger when cooled to room temperature.
“This is therefore a win-win for more economical energy and for the environment,” Sal said.
Interesting potential in the aerospace sector
Researchers said the findings could benefit industries other than energy. Aerospace researchers are looking for lightweight materials that can withstand high temperatures. Furthermore, Ames Lab scientist Nic Argibay stated that Ames and Sandia are collaborating with the industry to investigate how alloys like this could be used in the automotive industry.
Argibay also highlighted the research team’s work to develop a new class of alloys to address manufacturing and scalability challenges, adding that the electronic structure theory pioneered by Ames Lab was able to provide insight into the atomic origins of these valuable features.
What the discovery means to the future of 3D printing & materials science
This new study shows how the technique can be used to create novel materials quickly and effectively. Members of the Sandia team used a 3D printer to swiftly fuse together metal powders and create a sample of it.
Because no single metal comprises more than half of the material, Sandia’s invention also signifies a fundamental change in the way alloys have been developed. In contrast, the composition of steel is roughly 98 per cent iron mixed with carbon and other components.
“Iron and a pinch of carbon changed the world,” Sandia scientist Andrew Kustas said. “We have a lot of examples of where we have combined two or three elements to make a useful engineering alloy. Now, we’re starting to go into four or five or beyond within a single material. And that’s when it really starts to get interesting and challenging from materials science and metallurgical perspectives.”
From here on, the team is interested in investigating cutting-edge modelling methods that could aid in the discovery of further materials that may belong to a potential new class of high-performance, additive manufacturing-oriented superalloys.