United Launch Alliance (ULA), the premier launch services company in the US, has supported America’s presence in space for more than 50 years with its heritage systems Atlas and Delta.
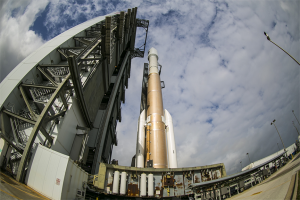
Image credit: investors.stratasys.com
The company has been in the costly business of making launch vehicles for NASA and the US Air Force for decades, constantly trying to drive down production costs by implementing innovative manufacturing technologies.
As of late, with the rapid emergence of 3D printing technology as a serious manufacturing tool, the ULA has been increasingly utilising 3D printing in its production processes to effectuate its vision to reduce launch vehicle costs by up to 50%.
ULA has recently acquired Stratasys’ Fortus 900mc 3D Production Systems and began the process of updating the Environmental Control System (ECS) duct on the Atlas V, which will launch with the new 3D component in 2016.
“It’s about as demanding an application as you can get,” says Rich Garrity, VP and General Manager Vertical Solutions Unit for Additive Manufacturing system maker Stratasys Ltd, in a press release.
“Rockets must endure pressure, G-force, speed, vibration, heat, and extreme cold.”
The previous design for the ECS duct, which is critical to the countdown sequence of a launch delivering nitrogen to sensitive electronic components within the rocket booster, contained 140 parts. By modifying the design using FDM 3D Printing Technology, ULA has managed to reduce the number of parts to only 16, which resulted in a 57% part-cost reduction and significant reduction in installation time.
Greg Arend, Program Manager for Additive Manufacturing at ULA, said the company selected the ULTEM 9085 FDM thermoplastic material to produce durable, high-performance end-use parts.
“ULTEM 9085 has great strength properties over a wide temperature range,” Mr Arend said.
“We have done testing to show that it is very capable of withstanding temperatures from cryogenic all the way up to extreme heat. And it’s tough enough to handle the vibration and stress of lift off and flight. We’re very satisfied with its performance.”
The Atlas V will not be the last launch vehicle incorporating 3D printing technology, with ULA planning to increase the quantity of 3D printed parts to over 100 on the next generation rocket.
“We see somewhat of an exponential growth in the utility of 3D printing for flight applications on our current vehicles. And we intend to use it heavily with our Vulcan rocket,” Mr Arend said.