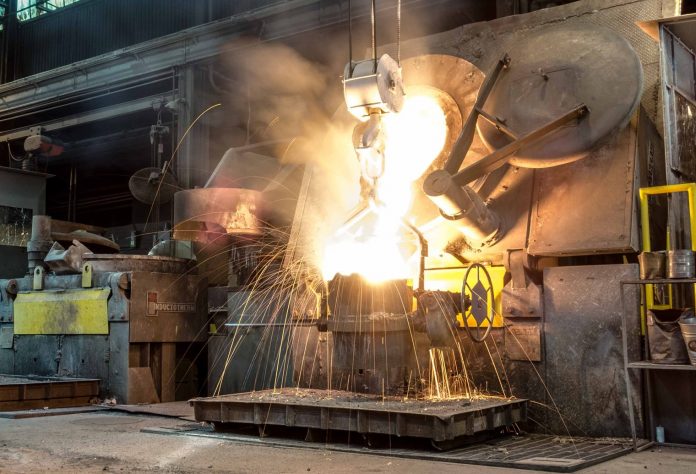
It takes a while, but sometimes old dogs do learn new tricks. JC Steele & Sons (known Down Under as Steele Australia) has been a leader in the stiff extrusion industry for 130 years. Recently they boasted a 75% expense reduction and 50% increase to annual production in their sand casting operations. The change came…