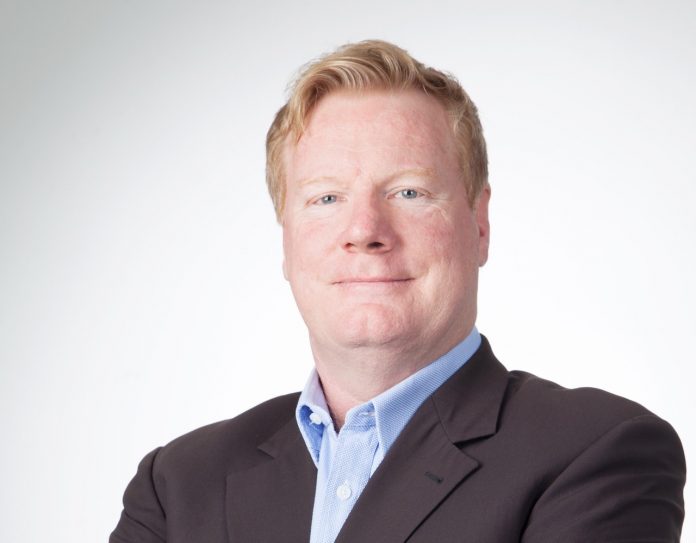
This article is by Dr Rob McCartney, CEO of occupational health specialists Resile As the COVID-19 crisis impacts on businesses across Australia, it is essential the manufacturing industry is proactive about putting strategies in place to protect the health of workers and safeguard the continuity of operations. Education of workers, risk minimisation and risk management…