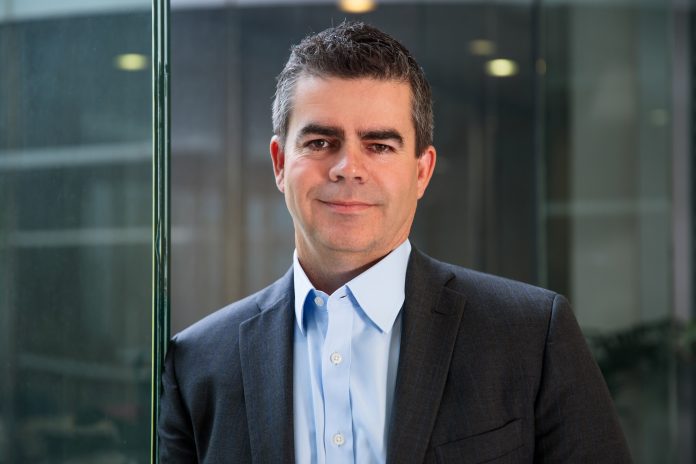
Article by Adrian Leach, CEO of World Travel Protection When the first lockdowns as a result of the COVID-19 pandemic began nearly a year ago most of us found ourselves in a blur of work as we frantically rushed to establish new working norms. With our workforces being forced in most instances to stay home…