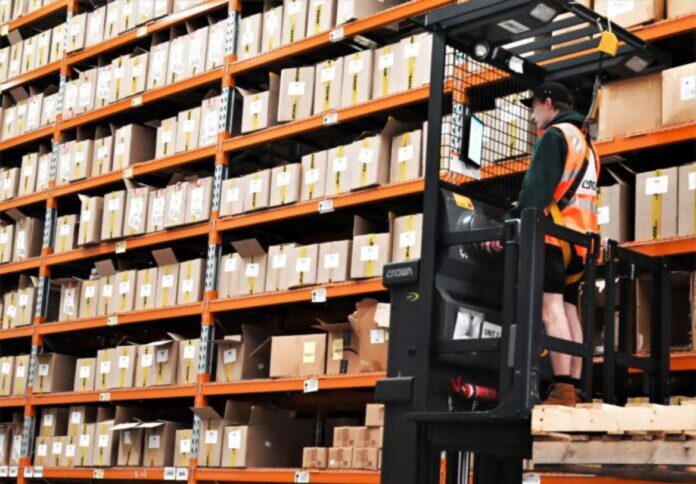
Sponsored content byAccess Mintsoft
Many manufacturing leaders are increasingly realising the role of streamlined order management in coping with increasing orders, supply chain disruptions, and catering to customer demands for faster fulfilment.
From inventory and fulfilment tracking to analytics and reporting, order management involves multiple complex processes that must align to deliver a great customer experience. These processes enable manufacturers and retailers to harness inventory data to provide real-world insights.
To stay on top of things in today’s increasingly competitive and fast-paced industry, business leaders are turning to order management systems (OMS) to automate their daily activities.
Read on to discover more about the 5 key reasons manufacturers, retailers and 3PLs need an efficient OMS tool:
Remove the manual
Research from the Harvard Business Review reveals that warehouse workers see automation as key to helping them produce higher-quality work and free up their time to focus on higher-value tasks.
Unlike human employees who are only able to see what is directly in front of them, OMS tools are designed to connect real data between systems to reduce errors and streamline operations. These systems connect data from carriers, drop-ship locations, suppliers, and more to make sure every member of the supply chain is interfacing efficiently and effectively.
Software solutions, like Mintsoft, remove the need to manually monitor orders coming in by providing updates in real-time as they are received, all the way through to the shipments being dispatched within the platform.
“We didn’t use the automated batching feature for quite a while and every single day at morning, lunch and in the afternoon, someone on the team would sit down and make up all the batches that had come in. That was three hours of someone’s day, every single day. Across a week, month and year, that’s huge. That’s a third of someone’s work time taken up with manual tasks we were able to automate with Mintsoft,” said Mack Blunsom, owner-operator of Black Bear Fulfilment, a third-party logistics company leveraging Access Mintsoft.
Centralised and scalable
A typical OMS is equipped with independent functions separated by individual tasks, providing each component with the information needed to facilitate its work in the overall function of the system.
These systems are designed to be scalable, thus allowing them to act as a shared interface across the supply chain. Integrations help trim down complicated processes and automate time-consuming tasks and entire workflows, which in turn saves time and removes the risk of human error.
Lower inventory costs
Businesses with an OMS can take control of inventory management by simplifying processes with automation processes. Users can easily move stock between locations with simple scanning for replenishment or putaway.
“The automation functionality makes everything a breeze. The solution is so good that I could quite literally grab someone off the street and have them trained up to be picking and packing within an hour, We’ve saved tones of time and money just with that one feature,” Blunsom added.
Drives data-driven decisions
Businesses equipped with a cloud-based OMS can automate unavoidable admin tasks, which drastically reduces errors, increases efficiency and helps make informed decisions.
Having complete visibility over business operations through a single platform provides deeper insights for forecasting and demand planning, allowing manufacturing and retail business leaders to ensure they always have efficient stock levels. It also means the risk of overselling – and disappointing customers – is eliminated.
Better organised warehouse operations
Keeping on top of inventory management and warehouse operations has been a painstaking process in the past. And with today’s rapidly evolving industry, this task can make or break a business, leaving customers unhappy, employees stressed, and profits cut.
To stay on top of things, manufacturers and retailers need a cloud-based OMS that acts as warehouse management software (WMS), allowing them to gain a complete overview of the warehouse, inventory, and courier relationships from a single platform.
Mintsoft is designed to automatically push out stock levels to all e-commerce channels at regular intervals, making sure inventory is synced. This is important for smaller online retailers that compete in this fast-paced and increasingly competitive industry, as it allows them to make gains wherever possible. Having an OMS means you can ensure your marketplaces are “staffed” even when you are not there.
Mintsoft is a cloud-based order fulfilment software designed to help businesses streamline their order processing for those in online retail and third-party logistics. The solution integrates orders from various online shopping platforms and sales channels, enabling manufacturing companies to manage the full dispatch process from picking, packing, and shipping.
To help you pick the right OMS customised for your business needs, visit Access Mintsoft’s Complete Guide to Order Fulfillment & Warehouse Management.