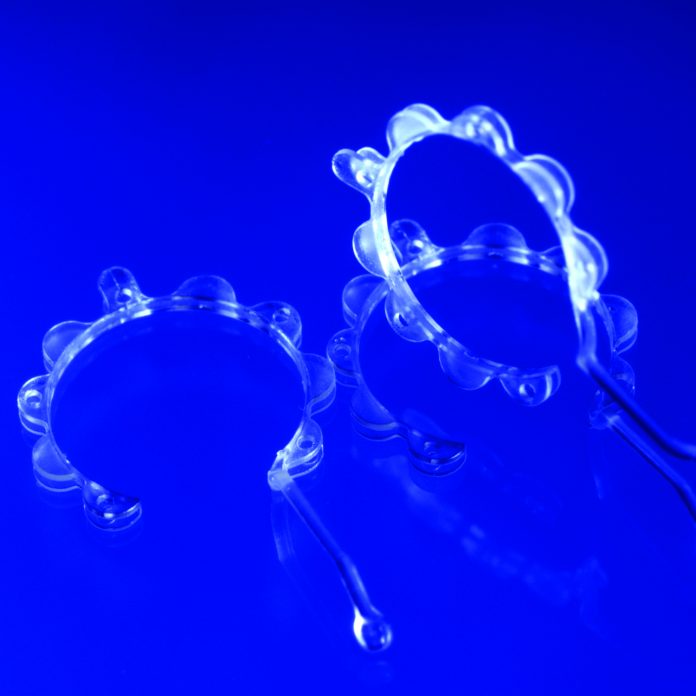
Media Release by Accumold
The medical device industry is constantly looking for smaller products and components with ever more exacting and often micron-level tolerances. The industry demands absolute precision, totally repeatable manufacturing processes, and zero failure rates for products that are frequently used in safety-critical applications. As such they must work alongside and partner with micro molding experts such as Accunold that are working at the cutting-edge of advanced design and manufacture.
At the MedtecLIVE with T4M event, Stuttgart, Germany, 3-5 May Accumold will be displaying an array of innovative medical parts and components on booth 237 in Hall 10 that it has manufactured over a long relationship with the medical device sector globally and through an innate understanding of the requirements of design for micro manufacturing (DfMM). The company is unique in that it is truly vertically integrated, and as such it is able to operate as a one-stop partner in the development and manufacture of medical devices and components. Under one roof, Accumold offers design and material assistance, micro tool fabrication, proprietary micro molding services, cutting-edge metrology, assembly, and automation, and this facilitates the streamlining of a customer’s medical product development process, and the attainment of optimal outcomes in terms of timeliness, innovation, cost, and accuracy.
Aaron Johnson, VP of Marketing and Customer Strategy, Accumold says, “We are proud to say that we have partnered with countless leading medical device manufacturers across the world, and with each we operate strategically to ensure that the product development process is as efficient as possible. Key to success is that medical device OEMs do not just view their chosen micro molder as a job shop, but rather that they partner with the molder at the earliest possible point in the design-to-market process in order to avoid costly mistakes. Micro medical plastic product manufacture requires that the relationship between OEM and micro molding specialist is a true partnership, but often run differently from a traditional OEM/supplier relationship. In micro manufacturing, most of the mission critical issues occur at the design and prototyping stage of product development. This can — and often does — include material choice and even packaging considerations. A true partnership will ensure faster time-to-market with more efficient and lower cost products.”
Micro molding for medical device OEMs is an art form honed after years of expertise and trouble-shooting, and it is vital that micro molders have the business culture, personnel, and equipment in place to provide the service necessary to ensure a successful project outcome.
Micro molders for medical device OEMs will be dealing with low, medium, and high volume runs in a variety of different materials, all requiring different levels of validation. They must also have the expertise in handling, storing, and processing often extremely expensive and sensitive materials that in many instances will be used in critical implantable applications.
Johnson concludes, “The heat is on for medical device OEMs to maintain profitability despite downward pressure on prices, and this can only be achieved through the development of innovative products that will fulfil the ever more exacting requirements of end-users. Demand will increasingly be for versatile devices that will embrace the potential for “smart” diagnostics and treatment presented by the proliferation of so-called “big data”; and devices that provide cheap alternatives to traditionally used but expensive diagnostic and therapeutic devices. Micro molding is today the solution used by many medical device OEMs to achieve their exacting manufacturing requirements, it being a technology that can produce tiny, complex, and feature rich components, efficiently, cost-effectively, and in volume. The correct use of micro molding technologies is today what gives successful medical device OEMs competitive advantage, and drives product innovation and profitability. Micro molding can provide high quality parts with high dimensional accuracy that are crucial for sensitive medical applications such as specialist devices for cancer treatment and diagnosis, small molded catheter tips, micro-needles, small surgical instruments, dental implants and infection control devices, and staples, to name but a few.”
Accumold wants to engage with any medical OEMs that will be at MedtecLIVE with T4M , and looks forward to meeting everyone to discuss how micro molding with Accumold can stimulate the manufacture of innovative medical devices in a timely and cost-effective fashion.