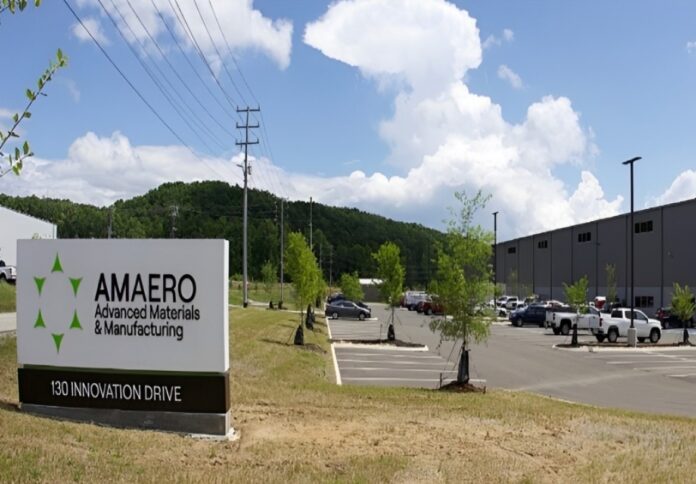
Amaero Ltd has announced a new technical development collaboration with Auburn University’s National Centre for Additive Manufacturing Excellence (NCAME), marking a key milestone in the company’s expansion into advanced metal additive manufacturing.
The partnership comes as NCAME’s recent testing has confirmed that Amaero’s proprietary powders – C103 and Ti64 (Ti-6AI-4V) – meet international industry standards, satisfying a critical qualification condition set by U.S.-based 3D printing company Velo3D.
The collaboration will combine Amaero’s advanced gas atomisation technology and proprietary processes with NCAME’s research and testing capabilities to support continued material development and refinement.
Initial projects undertaken through the partnership have demonstrated that material printed from Amaero’s C103 powder conforms with ASTM F3635, Class B, and Ti64 material meets AMS7015 and ASTM F3001 standards.
“The close collaboration between Amaero and Auburn University’s NCAME has demonstrated Amaero’s powder conformance with additive manufacturing industry standards,” said Dr Arun Jeldi, CEO of Velo3D.
“As a result of Amaero’s accelerated achievement, we are excited to announce that under the Velo3D–Amaero strategic partnership, 1,000 kilograms of Niobium C103 and Titanium powder will arrive on the Velo3D production floor in Q3 CY2025 to support critical projects in the aerospace and defence industries.”
Amaero confirmed that Velo3D has issued initial purchase orders for 500 kg each of C103 and Ti64 powders, both scheduled for delivery in the first quarter of FY2026.
These powders are essential materials for high-performance applications, particularly in the space and defence sectors.
“Amaero has commissioned the most advanced atomisation technology and has assembled a technical team with pioneering experience and proprietary know-how for gas atomisation of refractory and titanium alloys,” said Hank J. Holland, Chairman and CEO of Amaero.
“As we commence atomisation of development refractory alloys, integrate continuous improvement initiatives, scale production and look to further improve the unit cost economics, Auburn University’s NCAME will be an invaluable partner.”
Holland emphasised the broader implications of the collaboration, noting the importance of a strong domestic supply chain for metal additive manufacturing.
“To achieve the potential of metal additive manufacturing, it’s important that we have a vibrant domestic manufacturing and supply chain ecosystem… Amaero is doing its part.”