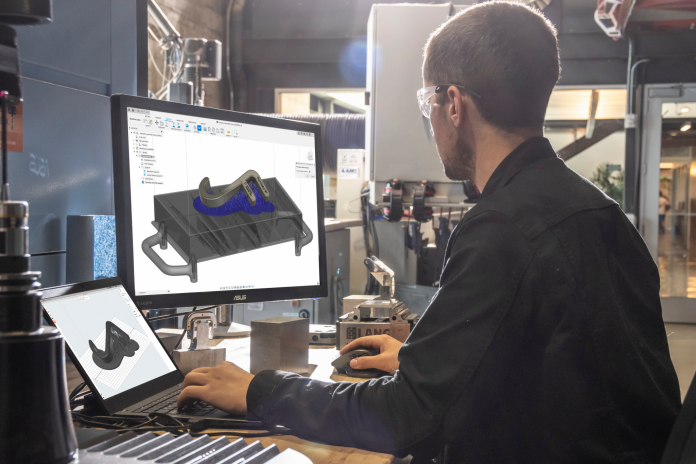
Sponsored Content by
The State of Desktop Additive Manufacturing
Autodesk and Formlabs are teaming up! You may not have noticed just yet, but Autodesk Fusion 360 has an expansive additive manufacturing workspace designed to help prototyping, researchers, additive engineers, designers and everyone else get the most control over their 3D printers.
Fusion 360’s additive manufacturing space is already a feature-rich space for FFF machines, with posts available for major manufacturers, along with fine support controls, assistive tools to avoid errors when printing, and even custom post configurators.
I can hear you asking, “Why would I want to use an additive manufacturing space when I have a dedicated slicer for my machine?” Excellent question! When using Fusion 360 for machining, you have the advantages of fully associative design and manufacturing data, so you can set up your manufacturing model once, then regenerate toolpaths any time you make a change to the design. In addition, Fusion 360 includes simulation tools that show you how your part will be made and assistive plugins to avoid mistakes before they happen.
Solutions and extending to SLA
Bringing these features over to additive manufacturing really expedites getting things made, opening you up to minimal file management and seamless collaboration with others. Already a high-performing 3D CAD tool for collaborating with others, the Additive Manufacturing Extension for Fusion 360 accelerates the AM phase of a project by folding additive experts into your workflow. More importantly though, Fusion 360’s additive manufacturing workspace essentially eliminates the need to create STLs for manufacturing by enabling you to push your data directly to your additive machine’s control software/slicer. Keeping the manufacturing data connected to the design data eliminates the need to constantly create new STLs in order to print.
Autodesk Fusion 360’s partnership with Formlabs brings these advantages to the full range of Formlabs SLA machines, giving you granular control over support structures, baseplates, and enabling you to push straight to a form file (with direct-to-PreForm coming soon). This partnership will also be extended to Formlabs SLS machines in the near future also!
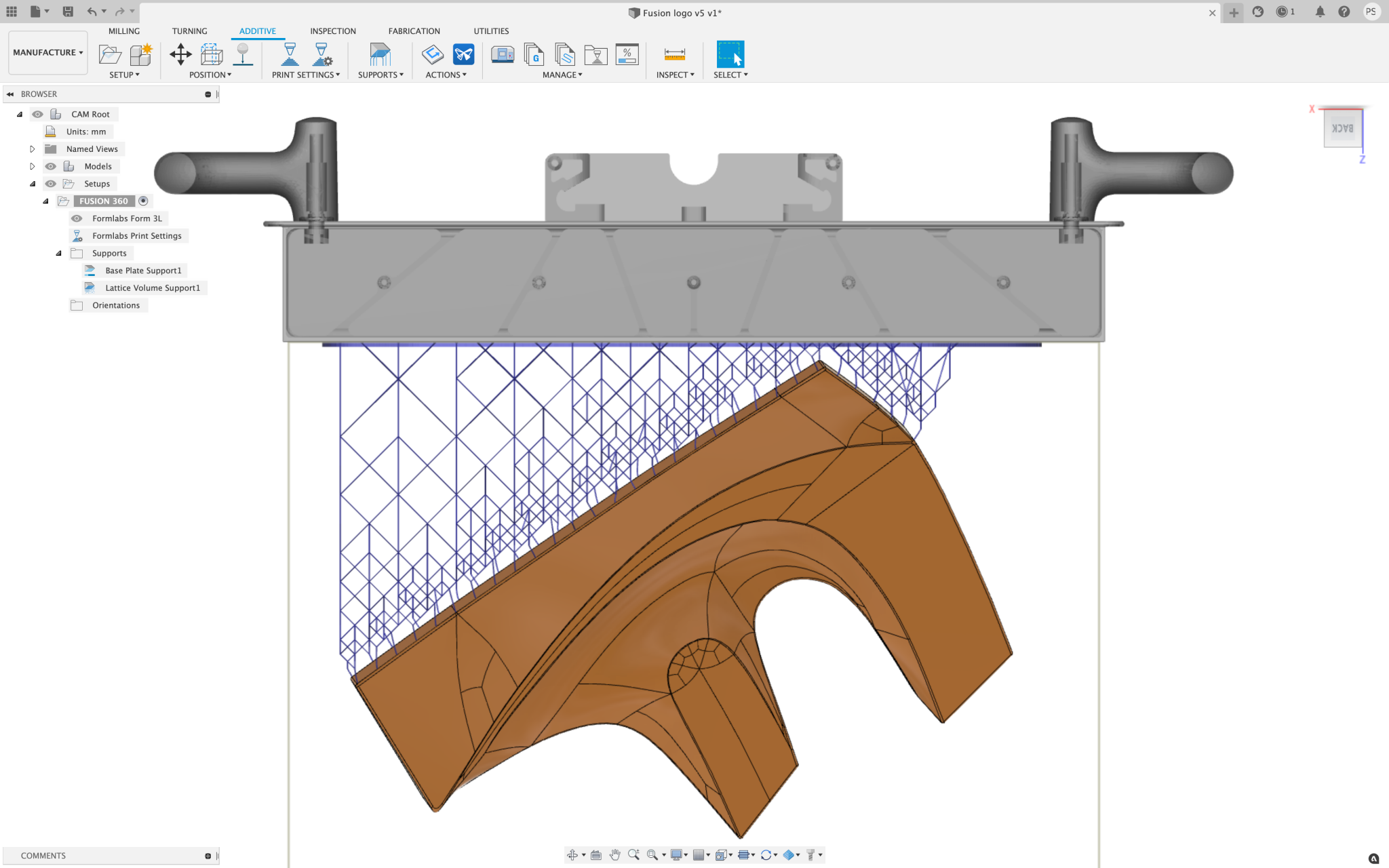
The Formlabs partnership also brings some quality-of-life features to speed up your time to printing. Auto Orient in Fusion 360 provides you granular control over what your priorities are for orientation. For instance, maybe you want support structures to have a higher priority over the footprint of the setup, or maybe the inverse, or something entirely different. The new Auto Orient feature will give you the ability to set your priorities, then review a number of options before sending to print.
Giving control to you, the user, doesn’t end here. This is v1.0 of Formlabs integration with Fusion 360. (Yes, 1.0; we’re not much for one-and-done at Autodesk.) You’ll also get more control over your support strategy for parts over using default slicers. With Fusion 360’s support strategies, you can now print with lattice supports made to your specifications, or use an entirely different support structure strategy, such as bar supports.
Talking to Sualp Ozel, Senior Product Manager for additive in Fusion 360, he explains that Autodesk’s focus is on eliminating barriers that slow commercial design and manufacturing. “When applications aren’t connected, productivity suffers, especially during design iterations, as change orders require several file translations and result in loss of detail.”
The Real World
Ok, that sounds wonderful, but does it work? The short answer to that is a resounding ‘yes,’ but don’t take our word for it. We recently sat down with a series of companies that use Formlabs and Fusion 360 to hear more about their workflows, and how Fusion 360 fits in.
Talking to Curtis Kennedy of Symbodi Labs, the company behind Vertiball, we learned that pairing Fusion 360 and Formlabs enabled them to expedite the entire design-to-manufacture workflow. The integration enabled Symbodi Labs to dramatically reduce time to manufacturing by creating accurate facsimiles that emulate the final injection molding manufacturing process. Fusion 360 in the mix minimized the total number of prototypes manufactured because they were able to validate “the theoretical functionality of a design through simulation” by taking advantage of Fusion 360’s centralized data philosophy. They brought together not just design and manufacturing, but simulation too.
Then there’s companies like Cosm Medical, which is tackling the very real challenge of mass customization needed in the medical industry. Cosm Medical produces prosthetics to treat pelvic floor disorders, which nearly half of all women will experience by age 80. As you can imagine, producing prosthetics for internal use is extremely challenging. Under current circumstances, most patients will go through an extensive process to find the one prosthetic, from 50 standardized designs, that fits properly. Cosm Medical produces prosthetics that fit first time by combining 3D scanning technology, Fusion 360 technology, and Formlabs technology.
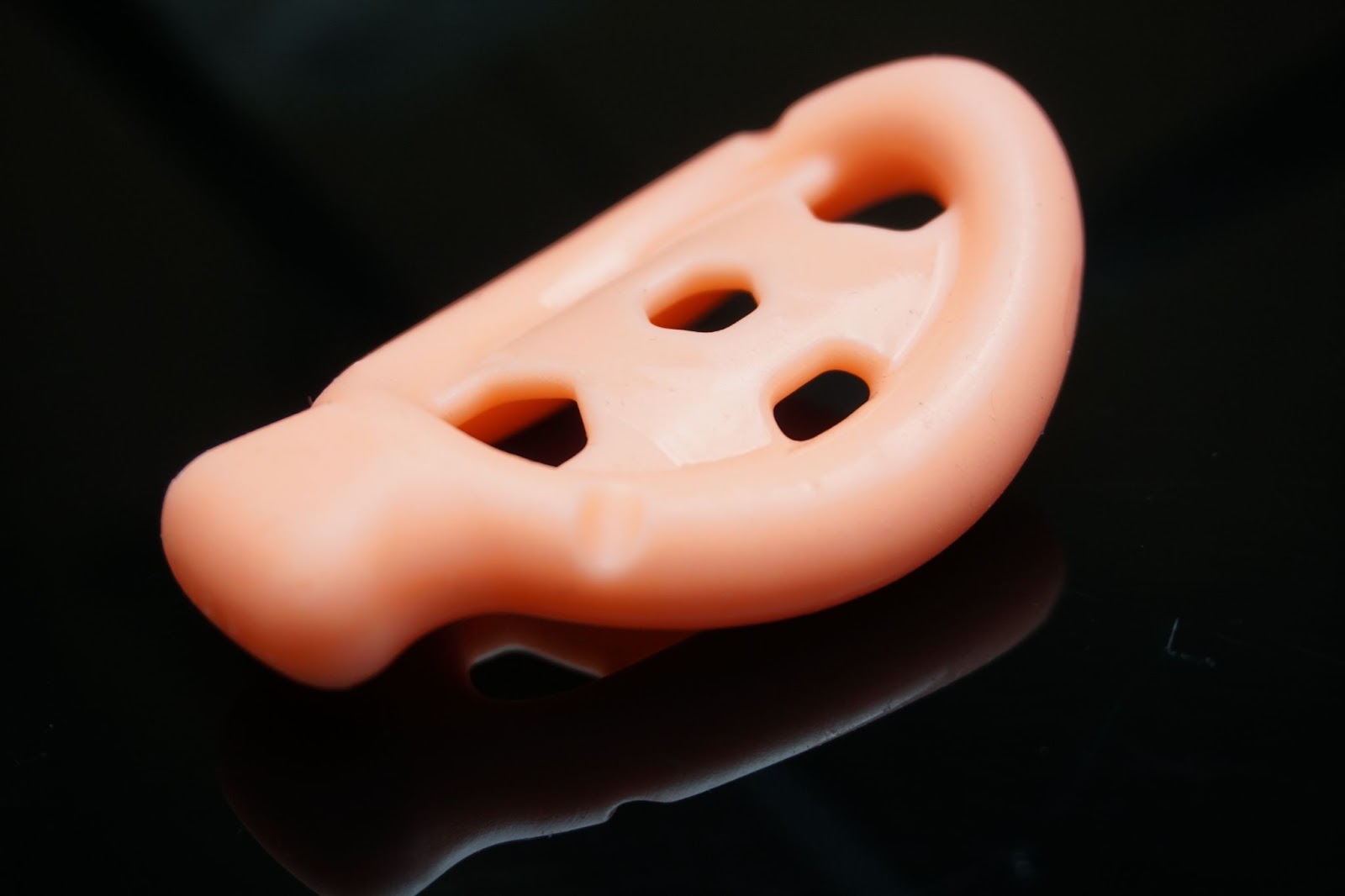
“Fusion 360…covers several steps in our process. It’s able to take in our sizing measurements from patients and build a patient-specific model and mold for our device utilizing parametric modelling. It can then export our molds to load into PreForm, so it’s fast and easy to get our molds printed. This entire process ensures the economic viability of our product in the long-term by automating many steps in the custom device design process.” Robert Lancefiield, tell us, Mechanical Engineer at Cosm. The Formlabs Form 3B 3D printer provides high-quality prints with a surface quality that enables Cosm Medical to go straight to silicone mold from the print, so patients get the best fitting prosthetic, first time.
We’re extremely excited by this partnership with Formlabs, and we can’t wait to show you what other wonderful features we’re bringing to close the gap between design and manufacturing in the near future. If you’re interested in receiving a free sample part from Formlabs, or better understanding what this partnership will provide you, then for more information visit www.autodesk.com/fusion360-formlabs.
Already a Fusion 360 user and Formlabs owner? You can print your own sample part directly from Fusion 360 and try out these new features.
Interested in trying out Fusion 360 and its Formlabs integration for yourself? Download a free trial right here.