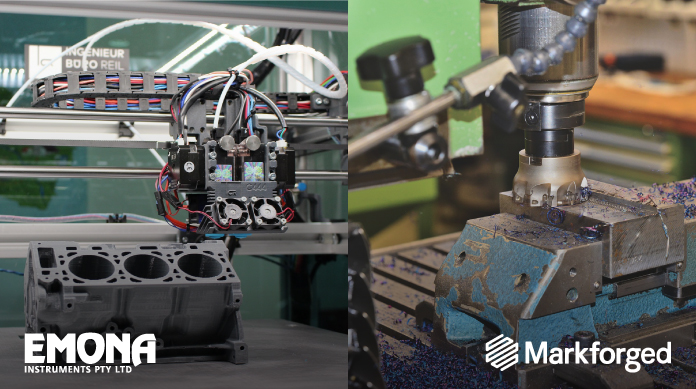
One of the most debated topics in today’s manufacturing industry is whether existing technology like traditional CNC manufacturing should be replaced with more advanced systems like 3D Printers. While 3D Printing could save manufacturers a significant amount of time and money, in some primary aspects of the manufacturing process, CNC continues to be the best application.
There is no definite answer to this debate, but maybe the most realistic solution is that manufacturers should combine both technologies.
In particular, a recent Whitepaper by Markforged acknowledges that both CNC and 3D technology have their own unique benefits, drawbacks and different roles to play in the manufacturing process. But when both technologies are used simultaneously, they can complement each other in the overall design and manufacturing workflow.
To make the best comparison and conclude the most efficient technology, this article explores how each technology performs in the five most important factors in a manufacturing process.
Subtractive Manufacturing vs Additive Manufacturing
Put simply, 3D Printing is an additive process, while CNC machining is a subtractive process.
CNC (Computer Numerical Control) machines begin with a solid block of material and, with sharp rotating tools, cuts the material into the desired final form. CNC machining has many benefits, including high dimensional precision and is adaptable to suit a wide range of components, such as wood, metals, and plastics.
Whereas the additive manufacturing process builds three-dimensional products one layer at a time. This technology is more fluid as there are many types of 3D Printers, each with different systems and materials.
In general, there are three leading additive manufacturing systems that builds 3D parts from either fused layers of thermoplastic materials, photopolymers cured by a light source, or powdered materials from starches to plastics or metals. The benefits of 3D Printing includes design freedom, applications in a wide range of industries, precision, speed, and potential to reduce costs and weight in components.
Design Freedom
In general, CNC manufacturing is still the go-to option for products that must be incredibly strong and robust, as well as have a high level of heat, and chemical resistance.
But modern 3D printing technologies do not have the same design constraints as a CNC machine. Because of its layered additive technique, 3D Printing is the best option for producing complicated objects, such as difficult undercuts, custom processing tools and fixtures, hollow parts, or organic shapes. As such complex fabrications would be impractical or prohibitively costly to produce with a CNC machine.
Measuring Precision
After design freedom, the next most important consideration in the manufacturing process is precision, including system accuracy, repeatability and resolution.
While 3D printers provide a high level of accuracy in layering, with resolutions of ±0.005 inch and an average tolerance of ±0.0015 to ±0.0035. In terms of precision, CNC machining is superior to all 3D Printing processes, their usual tolerance errors are around ±0.005 inches at the most standard level but can reach ±0.00005 inches on highly specialised machines.
Precision fluctuates more in 3D Printing because materials are printed layer by layer and use various materials, making them less accurate than CNC machines. But higher-quality industrial 3D printers can deliver precision that rival CNC machined parts and at a lower cost per part.
Material Compatibility
One CNC machine can work with nearly any material if the proper tooling is used. Most commonly, plastics such as PVC and Nylon 6/6, and metals such as aluminium, brass, zinc, bronze, stainless steel, tungsten, etc.
On the other hand, one 3D Printer is more limited with material compatibility. Its system can only use a set range of materials, and often the standards printers only print photopolymers or thermoplastics. Although newer 3D printers are much more flexible and can print parts with metal materials, but such newer machines are still in their infancy, making the technology more costly and unreliable.
Wasted Materials
CNC machines produce a lot of wasted material and non-reusable scraps due to their subtractive manufacturing process. As a result, the manufacturers pay for more material than they need.
Except for structural supports – which are optional – there is little to no waste during the whole additive manufacturing process. Less unused waste also makes 3D Printing more environmentally friendly.
Part Costs
Price-per-part takes into account a number of considerations such as material costs, tooling needs, equipment maintenance and operator wages.
CNC manufacturers often purchase more inventory than is needed, with high material wastage, job-specific tooling, and more skilled operators whose pay rises with skill level.
Whereas 3D printers are somewhat less costly to purchase, maintain, and operate. As operation can occur remotely, which saves costs on wages, lowers material costs, produces less material waste and lowers power requirements for operation.
However, additional factors make comparing the cost-per-part between the two technologies more difficult as 3D Printing is best for low-volume manufacturing, but CNC machining sees attractive economies of scale once quantities are larger.
The Bottom Line: Will 3D Printers Ever Replace CNC Machining?
Hence, the topic is not as easy as a one-to-one machine substitution, and no one technology can fix all manufacturing issues immediately.
Overall, the biggest distinction between the two technologies depends on the specific material, geometric complexity, manufacturing volume and budget of your part production. Manufacturers see quick returns on their investment into 3D printing manufacturing.
In general, manufacturing works best when both technologies are utilised within their strengthens, as they complement each other and cater to different part outputs.
But to determine the most appropriate technology for your specific manufacturing process, you should contact a local manufacturing expert for their advice. Emona Instruments is the leading Australian reseller of Markforged Industrial 3D Printers and 3D Materials. We cater for a range of budgets, functions and technologies, suitable for R&D professionals, production lines or the classroom.
From Markforged Carbon Fibre Composite and Metal 3D Printer’s printing in stainless steel, tool steel, copper and Inconel, through to Formlabs SLA 3D Printers printing resin. Contact the Emona team for more expert information and technical support on (02) 9519 3933, email testinst@emona.com.au or visit Emona Instruments.