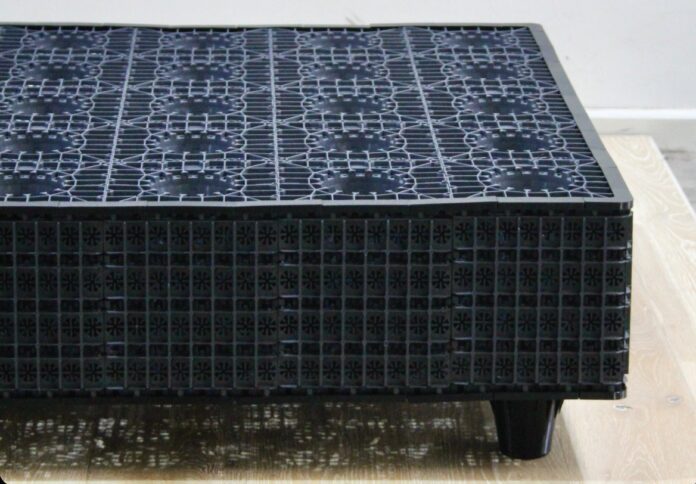
A new wave of innovation is transforming the Australian manufacturing sector, with sustainability at its core. ROBOVOID, in collaboration with Swinburne University, GT Recycling, and Sustainability Victoria, has developed a groundbreaking bed base made entirely from recycled plastic.
This project, known as Circular Beds, is an industry-first solution addressing landfill waste while setting new performance and durability benchmarks for bedding products.
In an exclusive interview with Australian Manufacturing, Scott Olding, director of ROBOVOID, and Shannon Smyth, manager of Markets Acceleration at Sustainability Victoria, shed light on how innovation and collaboration are reshaping the bedding industry with Circular Beds.
Redesigning the bed base for a circular future
“We started with a challenge – how do we redesign bed bases to keep them out of landfill and make them a truly circular product?” said Scott Olding, director of ROBOVOID. With prior experience in environmentally focused solutions, including 100 per cent recycled plastic void formers for concrete construction, the team faced new technical hurdles in the bedding industry.
Traditional bed bases, often made of wood, are difficult to recycle due to their composite materials. ROBOVOID sought to change this by designing a product that prioritises reuse first and recycling at end-of-life.
“We needed a bed base that was made entirely of the same recycled plastic material, including the legs, and could be reused and reconfigured,” Olding said. He noted the bed base had to resist odour, mould, and pests, be easy to clean, and fully recyclable.
Developing the product required new tooling, rigorous laboratory testing, and real-world trials, from student accommodations to NRL athletes’ residences. Olding added, “We could have saved time and money if we accepted that some of the components of the bed base didn’t need to be made from the
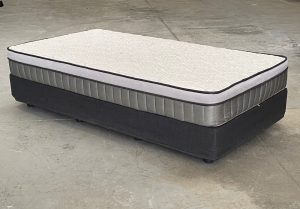
same single recycled plastic material – but that was not something we could accept with our design!”
Another key advantage of circular beds is modularity, allowing users to reconfigure the bed from a single to a double, queen, or king-size as their needs change. “This significantly extends its lifespan without adding to waste streams, reducing annual waste management costs,” Olding added.
Collaboration: A key driver of innovation
The project was brought to life through partnerships with Swinburne University and GT Recycling. Olding said Swinburne offered research support and testing facilities, while GT Recycling supplied quality recycled plastic.
The initiative also received support from Sustainability Victoria and the Australian Bedding Stewardship Council. “A.H. Beard also provided access to and use of their testing facilities, in particular their industrial scale Rollator testing machine,” he added.
A sustainable future for Australian manufacturing
The Circular Beds project aligns seamlessly with Sustainability Victoria’s broader vision of a circular economy. “One of Sustainability Victoria’s focus areas is accelerating new markets for recycled materials,” said Shannon Smyth, Manager, Markets Acceleration at Sustainability Victoria. “The Circular Beds project is a fantastic example of what’s possible, even in unexpected sectors.”
Sustainability Victoria has actively supported this initiative through its Circular Economy Research and Development (R&D) Fund. “A $2.7 million funding package through the Circular Economy Research and Development (R&D) Fund – Materials was provided to research institutes to partner with industry to develop new uses for recycled priority materials,” Smyth explained.
Industry impact and lessons for circular manufacturing
Australia disposes of approximately 1.8 million mattresses and hundreds of thousands of bed bases each year, with many ending up in landfill. “This is an Australian-first and could be a game changer for the bedding industry,” Smyth remarked.
He noted that with backing from the Australian Bedding Stewardship Council, the project highlights how bed bases can be sustainably produced using only recycled materials while ensuring long-term durability.
A win-win for industry and the environment
Since its inception, Olding said that ROBOVOID has aimed to develop commercially viable, environmentally impactful solutions. He explained that manufacturing 10,000 King Single-size Circular Beds requires 22,000 kg of recycled plastic, effectively preventing this material from ending up in landfill and keeping it within the circular economy.
As demand for sustainable solutions continues to rise, initiatives like Circular Beds highlight the power of engineering, collaboration, and forward-thinking design in building a more sustainable future.
The content of this article is based on information supplied by ROBOVOID and Sustainability Victoria. Please consult a licenced and/or registered professional in this area before making any decisions based on the content of this article.