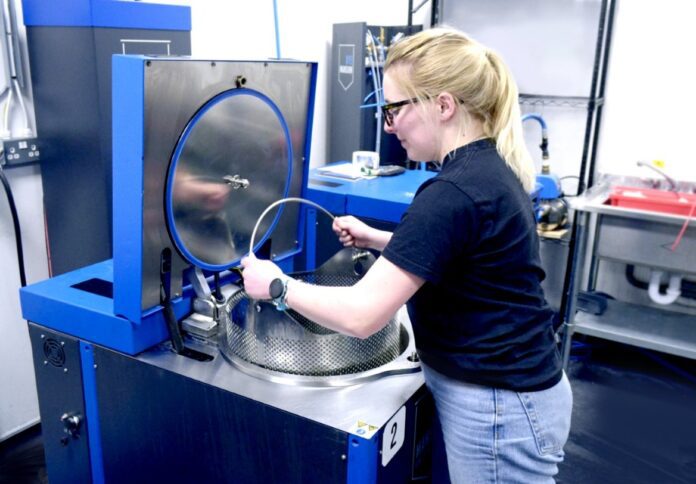
While the printers serve as its workhorses, the post-processing and dispatch division at London-based 3DPRINTUK is the “beating heart of the company” because of its operating system created in-house to enable a quick sorting of components and to indicate to users which part has what finish, says order manager Rebecca Wilkes.
The 3DPRINTUK official said the process is extremely user-friendly and easy, allowing teams to go through builds or dye batches as quickly as we do while maintaining quality.
The 3D printing bureau also laid its plans to officially launch its new finishing hub later this year, further adding touches to the dyeing, polishing, and shot peening it already offers.
“My team is responsible for reporting any parts we come across while sorting from any post-processing that are not conforming to our quality policy,” Wilkes said.
The 3D printing bureau official said all of this must be recorded so that quality managers can report these parts and investigate further if necessary.
Since 3DPRINTUK gets thousands of components every day, Wilkes pointed out that the company can most likely identify a problem that is occurring more frequently than it should.
Meanwhile, being awarded the ISO 9001 certification was a tremendously exciting time for the business, according to Wilkes, since it solidified the idea that all of its effort leading up to the audit had been worthwhile.
“Having this certification will really open up a lot of new opportunities for us which is exciting and will only help to grow the company, which is always the goal for us,” Wilkes noted.
Another aspect of working at 3DPRINTUK that makes Wilkes very proud is that they are led by Director Nick Allen.
Wilkes emphasised that Allen has built an environment where everyone is working toward the same objective – to thrive and go above and beyond to achieve success.
“We are producing a high quantity of parts every single day just like any other big bureau would, but I think what sets us apart is that we treat every order that comes through the door with the same care and attention to detail no matter the value or volume of parts,” explained Wilkes.
Currently, Wilkes said that the 3D printing bureau is continually searching for ways to improve its services and expand its technology so that it can provide the finest service possible to its customers.