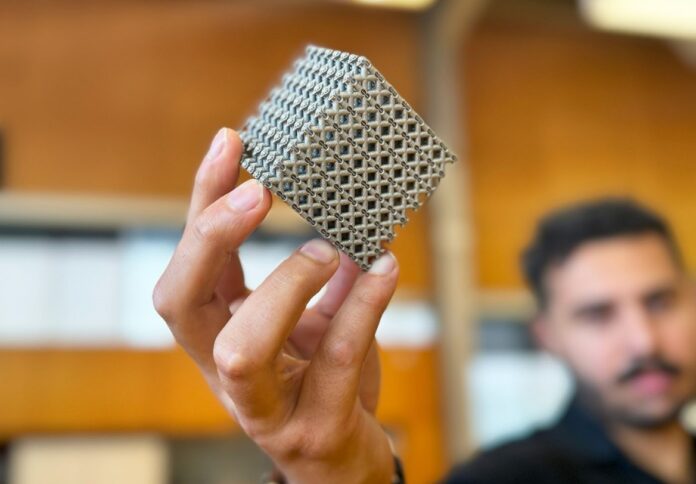
RMIT University researchers have crafted a new metamaterial from common titanium alloy using 3D printing, showcasing unprecedented strength-to-weight proportions never before witnessed in natural or manufactured materials.
This breakthrough material could potentially revolutionise the manufacturing processes of various products, from medical implants to aircraft or rocket components, the researchers said in a news release.
Published in the journal Advanced Materials, the research unveiled a lattice structure design that sets this material apart.
Testing revealed it to be 50 per cent stronger than the next most robust alloy of similar density used in aerospace applications.
Inspired by nature’s own design principles, particularly the strength found in hollow-stemmed plants and corals, RMIT’s team led by Distinguished Professor Ma Qian sought to overcome the limitations of traditional manufacturing methods.
These methods often resulted in stress concentrations within hollow structures, leading to premature failures.
Professor Qian explained, “For most topologies, it is common for less than half of the material to mainly bear the compressive load, while the larger volume of material is structurally insignificant.”
Metal 3D printing offered a solution to these challenges. By pushing the boundaries of design, the team developed a lattice structure optimised to distribute stress evenly, thereby enhancing its strength and structural efficiency.
“We designed a hollow tubular lattice structure with a thin band running inside it,” said Qian.
“These elements together exhibit unprecedented strength and lightness, surpassing what is found in nature,” the researcher added.
The lattice structure, printed using laser powder bed fusion at RMIT’s Advanced Manufacturing Precinct, demonstrated remarkable strength.
Compared to the strongest available cast magnesium alloy, it showed a 50 per cent increase in strength and reduced stress concentration on weak points, effectively deflecting cracks along the structure.
Lead author Jordan Noronha, a PhD candidate at RMIT, highlights the material’s versatility in terms of scale and potential applications, from medical implants to aerospace components.
“Compared with the strongest available cast magnesium alloy currently used in commercial applications requiring high strength and light weight, our titanium metamaterial with a comparable density was shown to be much stronger or less susceptible to permanent shape change under compressive loading,” Noronha stated.
While the material exhibits resistance to temperatures up to 350°C, further advancements could extend its applications into higher-temperature environments, such as aerospace or firefighting drones.
Milan Brandt, the technical director of RMIT’s Advanced Manufacturing Precinct, is inviting collaboration from interested companies, emphasising the collaborative and problem-solving approach of the research team.