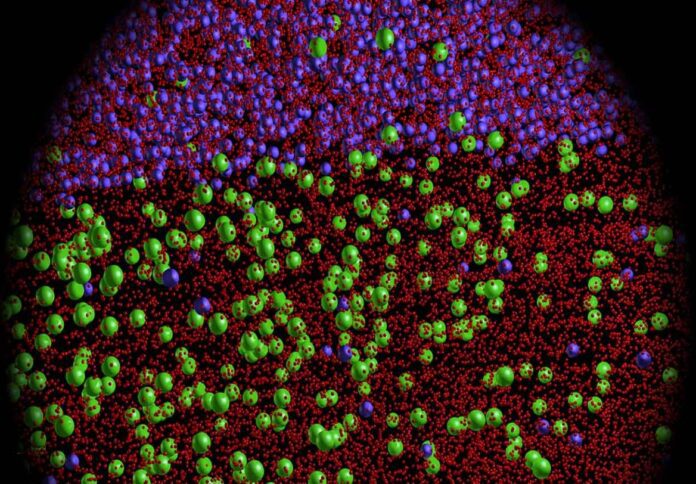
A team of researchers from RMIT University and the University of Sydney has developed a new class of ductile and strong titanium alloys using a combination of alloy design and 3D printing.
The breakthrough, published in the top journal Nature, could help extend the applications of titanium alloys, improve sustainability, and drive innovative alloy design, RMIT revealed in a press release.
The scientists said their discovery holds promise for a new class of more sustainable high-performance titanium alloys for applications in aerospace, biomedical, chemical engineering, space and energy technologies.
The study was done in collaboration with Hong Kong Polytechnic University and Melbourne company Hexagon Manufacturing Intelligence.
Lead researcher Distinguished Professor Ma Qian from RMIT said the team’s design included circular economy principles, and this holds tremendous promise for making their novel titanium alloys from industrial waste and low-grade materials.
“Reusing waste and low-quality materials has the potential to add economic value and reduce the high carbon footprint of the titanium industry,” said Qian from RMIT’s Centre for Additive Manufacturing in the School of Engineering.
In particular, the team used Laser Directed Energy Deposition (L-DED), a 3D printing process ideal for making large, complex parts, to print their alloys from metal powder.
“A key enabler for us was the combination of our alloy design concepts with 3D-printing process design, which has identified a range of alloys that are strong, ductile and easy to print,” Qian said.
The research team underscored that the attractive properties of these new alloys that can rival those of commercial alloys are attributed to their microstructure.
“This research delivers a new titanium alloy system capable of a wide and tunable range of mechanical properties, high manufacturability, enormous potential for emissions reduction and insights for materials design in kindred systems,” said co-lead researcher and the University of Sydney Pro-Vice-Chancellor Professor Simon Ringer.
Meanwhile, RMIT Vice-Chancellor’s Research Fellow and lead author Dr Tingting Song stated that the team is “at the start of a major journey, from the proof of our new concepts here, towards industrial applications.”
“There’s a potential opportunity for industry to reuse waste sponge titanium-oxygen-iron alloy, ‘out-of-spec’ recycled high-oxygen titanium powders or titanium powders made from high-oxygen scrap titanium using our approach,” Dr Song noted.
The finding has larger ramifications, according to co-lead author Dr Zibin Chen, who joined Hong Kong Polytechnic University from the University of Sydney later in the collaboration.
“Our work may provide a template to mitigate these oxygen embrittlement issues through 3D printing and microstructure design,” Dr Chen said.