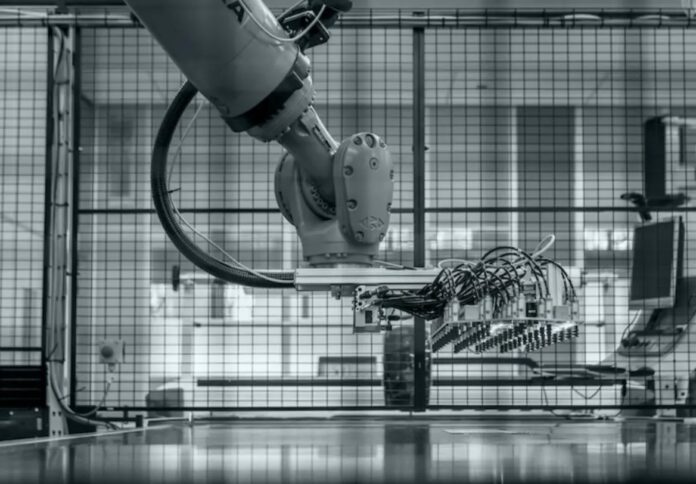
Technology solutions company Sparc Technologies Limited has shared an update on its collaboration with the Queensland University of Technology (QUT) to develop a sustainable hard carbon anode material for sodium-ion batteries (SIBs).
The ASX-listed company said that QUT has delivered the first project milestone report, which details the outcomes of SIB half-cell battery testing as well as material characterisation for a sustainably sourced anode material under various processing settings.
While more optimisation, testing, and process development work must be done, reversible capacities for a batch of materials tested under the same conditions surpassed 535mAh/g and averaged 477mAh/g over five trials.
Furthermore, with China being the world’s major supplier of hard carbon materials, Sparc said the QUT-led approach intends to provide an alternate western supply of anode materials, decreasing sovereign risks for SIB cell manufacturers.
Stephen Hunt, Sparc Technologies executive chairman, said the company is very encouraged by the positive results from its research effort with QUT into the development of sustainable hard carbon anode materials for sodium-ion batteries.
“The combination of green bio-waste feedstock and faster, less energy-intensive processing with a very high capacity anode material offers attractive potential for further research and development,” Hunt remarked.
He continued, “Equally as exciting is the continued progress of sodium-ion batteries towards commercialisation as evidenced by recent activities of major global battery producers including CATL, BYD and Reliance Industries.”
Sparc Technologies, being one of the few ASX-listed firms actively pursuing sodium-ion batteries, puts the company in a good position, according to Hunt.
The company also emphasised that a high-performance, low-cost, sustainably derived anode material for SIBs will fill a gap in emerging alternative battery technology.
In particular, the hard carbon samples have been materially characterised using a variety of characterisation techniques (XRD, XPS, Raman, TEM, SEM, and BET).
This will serve as a basis for comparison in subsequent test work, such as the trialling of different feedstock sources and process parameters, the company noted.
Electrochemical techniques such as galvanostatic charge/discharge – capacity and cycle stability – have been used to examine the performance of sodium ion battery samples (in half-cell configuration).
Moreover, to guarantee the repeatability of the measurements, many coin cells (five cells for each hard carbon sample) were fabricated for each electrode.
Commercial mass loadings and low C-rates (0.05) were also employed.
Future work will examine strategies to increase initial coulombic efficiency, evaluate cycling stabilities up to 500 cycles, and construct and test entire cells.
Sparc continues to work on the project with a knowledgeable battery consultant and has around six months left in the research program with QUT.
In the upcoming months, Sparc plans to use life cycle analysis and economic modelling to further investigate the scope of energy and cost reductions that can be realised by employing the proposed processing approach rather than the current hard carbon materials.