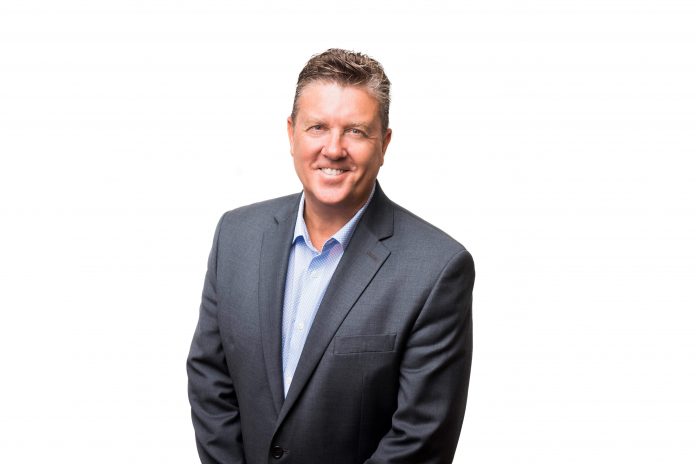
This article is by Rob Stummer, CEO Asia Pacific, SYSPRO With the globalisation of markets and economies the world over, it is common practice for companies to rely on low-cost manufacturers in cheap labour markets. However, the impact of the coronavirus and the disruptions that many companies have experienced in their global supply chains will…