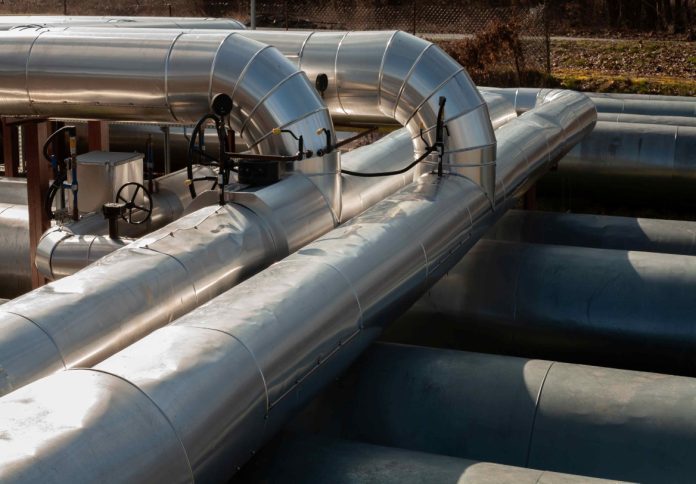
Article by Dave Dyer, technical sales engineer at Global Heat Transfer
Sustainability is no longer just a buzzword but an essential strategy for facilities managers looking to reduce operational costs and improve their environmental impact.
According to the International Energy Agency (IEA), industrial heat accounts for two-thirds of industrial energy demand and nearly one-fifth of global energy consumption, making it a key area for efficiency improvement. By optimising heat transfer systems, facilities managers can reduce their energy usage while driving sustainability. Here, Dave Dyer, technical sales engineer at thermal fluid specialist Global Heat Transfer, outlines practical steps to achieve this.
Thermal fluid systems face multiple operational challenges beyond just energy efficiency. One critical concern is the degradation of the fluid itself, which can occur when it’s exposed to high temperatures or poorly maintained systems. Without proper preventative measures, this degradation can escalate into serious safety and environmental hazards.
Retain more, use less
Uninsulated equipment in heat transfer fluid systems can waste substantial amounts of energy, leading to higher costs. For instance, if pipes carrying heated fluids aren’t properly insulated, they lose heat to the surrounding air. As a result, the system must work harder to maintain the desired temperature, increasing both energy use and the likelihood of thermal fluid degradation.
In a heat transfer system, certain areas are particularly prone to energy loss — such as piping and flanges. For example, flanges are joints connecting two pipes, which can allow heat to escape or even fluid to leak. Insulating these critical points prevents unnecessary heat loss, helping systems maintain consistent temperatures and reducing energy consumption.
Uninsulated equipment in heat transfer fluid systems can waste substantial amounts of energy, leading to higher costs. For example, if pipes carrying heated fluids aren’t properly insulated, they can lose heat into the surrounding air. As a result, the system works harder to maintain the desired temperature, increasing both energy use and the likelihood of thermal fluid degradation.
Research from the U.S. Department of Energy estimates that adding insulation to pipes can cut heat loss by up to 90 per cent, yielding significant cost savings over time. For maximum efficiency, using sprayed glass insulation which is non-porous is recommended, particularly for areas within 600 millimetres of flanges. Beyond this, standard materials like a rock-based mineral fibre product can complete the insulation.
After addressing these critical areas, additional measures such as valve and strainer jackets should be considered. These removable covers are designed to fit over specific components that help further reduce heat loss and protect equipment in high-temperature environments. Once insulation is in place, how can you confirm it’s performing as expected?
This is where thermal imaging comes in. By using infrared technology, thermal imaging cameras visualise heat retention and loss across a system, offering clear comparisons before and after insulation. This not only confirms insulation effectiveness but can also guide adjustments to boiler temperatures, improving overall energy efficiency.
By addressing heat loss through targeted insulation and using tools like thermal imaging, facilities managers can achieve significant savings while moving toward sustainability. However, energy efficiency must go hand in hand with system safety.
Preparing for the unexpected
While insulation helps reduce energy loss, facilities must also be prepared for the unexpected, such as oil spills. These incidents can pose environmental hazards and disrupt operations, so basic containment measures remain essential. Regular inspection of bunded areas and ensuring pill kits are accessible, with staff trained in proper response protocols, can help minimise risk and maintain safe working conditions.
One sometimes overlooked safety measure is the use of spray guards on flanges and valves. In the event of a leak or seal failure, even a minor release can cause high-pressure fluid to spray, creating hazardous conditions for personnel and increasing the risk of fire or equipment damage. Spray guards act as a vital containment solution, preventing this spray from escaping.
Modern spray guards are designed for both durability and performance, offering reliable protection while supporting compliance with international safety standards such as SOLAS regulations and the Model Code of Safe Practice IP15. These standards acknowledge that even fluids typically regarded as non-hazardous can become dangerous when released under pressure as mist or spray.
In systems using thermal fluids, where pressure and temperature are often high, spray guards offer essential protection against sudden gasket failure or unexpected leaks, helping facilities meet compliance requirements while protecting people, equipment and the environment.
Proper ventilation
Energy efficiency isn’t just about retaining heat, it’s also about ensuring systems operate optimally. Ventilation plays a critical role in keeping thermal fluid systems running efficiently and safely.
Expansion tanks accommodate changes in the volume of thermal fluid as it heats and cools but without proper ventilation the expansion tank gets too hot which oxides the fluid. The expansion tank vent should be piped to the ground floor into a vented dump tank. This setup adds an extra layer of safety, along with clear signage and restricted access to reduce fire risks and is located away from drains and water courses.
Inside heater rooms, airflow is essential. Installing louvre panels at different heights on walls, doors or windows ensures natural circulation of air, preventing heat buildup. For areas where structural modifications aren’t possible, electric fans or ducting can provide effective alternatives. For indoor expansion tanks, maintaining at least a two metre clearance around the tank ensures sufficient airflow and prevents overheating.
Each of these improvements, insulation, bunding and ventilation, contribute to more sustainable operations on their own. Together, they form a comprehensive approach that balances energy efficiency and environmental responsibility.
However, implementing these measures is only the beginning. Maintenance plans like Thermocare®, provide facilities managers with the tools and expertise they need to keep systems running at peak efficiency. By regularly sampling fluids to tailor system audits, equipment lifespan can be extended, downtime can be reduced, and overall sustainability can be improved.
Sustainability isn’t achieved overnight, but small, strategic changes can lead to transformative results. Facilities managers who focus on retaining energy, preparing for the unexpected and optimising airflow not only improve their environmental impact but also ensure operational efficiency and safety. By taking these steps and partnering with a thermal fluid experts, facilities managers can build a system that’s both sustainable and cost-effective.
Visit Global Heat Transfer’s website for more insights into optimising thermal fluid systems.
The content of this article is based on information supplied by Global Heat Transfer. This information is general in nature and has been prepared without taking your personal objectives, circumstances and needs into account. You should consider the appropriateness of the information to your own circumstances and, if necessary, seek appropriate professional advice. Consider the terms and conditions for the product before making any decision.