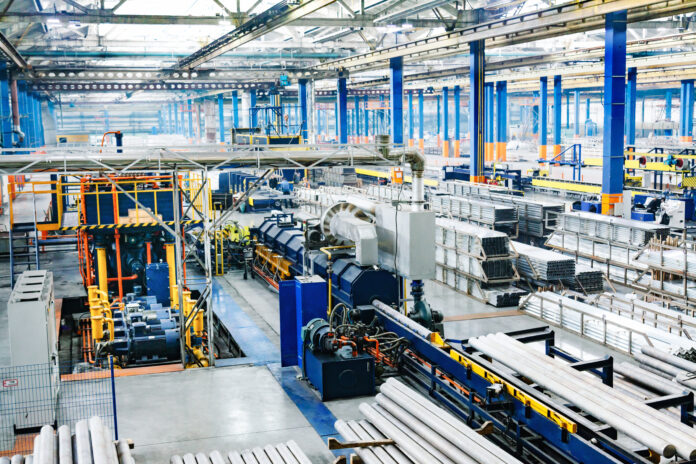
Article by Bill Haggerty, Principal, TRANSEARCH International Australia
Australian manufacturing is rarely going to be cheaper in the global market, so we need to be smarter to be more competitive. This is the reality that many within the industry are already aware of, which is driving more and more focus on innovative thinking and investment in streamlined processes and new technologies.
But what does this mean for those at the helm and what technical and human skillsets will managers need to adopt today and tomorrow to successfully implement these required changes?
With increasing rates of AI opportunities and adoption, Australian manufacturing leaders today need to not only be more efficient, resilient, ambitious, creative, and strategic, but people-centric.
In fact, successful manufacturing leaders for the coming decades must see human growth as essential to business growth.
Former Managing Director and CEO of the Innovative Manufacturing Cooperative Research Centre, David Chuter, says it is important leaders focus heavily on optimising their company by growing human capital in terms of both capability and capacity.
“It’s now their ability to collaborate, their ability to communicate, to motivate and to harness the talents of people around them and develop them so the people can be better than they thought they could be,” David said.
“This is what will deliver a value proposition to make people far more successful in a world where technology is rapidly moving forward.”
And it’s in this environment, successful manufacturing leaders are change agents who want to be innovative and have a transformative vision of the business that usually focuses on improvements, development, and consequently new products.
They shake things up to propel the business to the next level. They constantly question the status quo and move the company away from the ‘this is how we’ve always done things’ mentality, even when some employees resist the change.
“I think, when you think of change, change can bring both opportunity and risk and good leaders need to be able to manage both and identify what is the real opportunity. What is the real problem they can solve for customers?” David said.
Effective manufacturing leaders take every opportunity to spread that entrepreneurial spirit throughout the organisation to drive solutions that optimise the business.
But most importantly, Managing Director of the Advanced Manufacturing Growth Centre, Dr Jens Goennemann, believes a successful manufacturing leader needs to deeply understand what manufacturing is in the first place and needs to know how to answer a market need and deliver something customers truly value in the long term.
“The prevailing yet outdated view that manufacturing is comprised solely of production, or assembly, is simply not true. Manufacturing consists of seven steps across an entire manufacturing value chain, of which production is just one,” he said.
“If you’re an aspiring leader in this industry you understand that the ongoing advancement of manufacturing is an essential capability of a competitive company and the economy at large. It is also not about the items you make, but how you make them.
“Leaders need to drive their companies to be more globally competitive, hence by being better not cheaper. Look at successful manufacturing powerhouses like Germany or Austria, known for many good things but not for being cheap.
“The aim is for Australia to have a broad, vibrant, competitive manufacturing industry that can harness global opportunities in the first place, but also being in a position to respond to any type of crisis.”
The ability to anticipate where the market is going and be able to identify new technologies that will move their company forward in terms of business innovation and product development are other important traits a manufacturing leader should have.
They need to recognise the importance of cross-functional teams to shape the strategic vision of the company and need to be willing and capable of collaborating to drive new products and new solutions.
David said there was not one particular technology or one particular optimisation tool that leaders should be applying.
“They need to be across the breadth of all tools and technologies and work out which ones can bring the greatest value proposition to their business and into their supply chains,” he said.
“We need to pull ourselves back from a decline in productivity here in Australia. If we’re going to continue to build the manufacturing industry locally, it’s going to mean pulling a few levers.
“People, particularly leaders, are the ones that are going to take manufacturing forward in this country, so having a greater investment in developing people to a level where they can work in a very fast-moving world with lots of challenges, threats, new technologies, and processes and systems is vital.”
Harnessing innovative thinking via collaborative practices is another area of focus that should be top of mind for leaders.
They should embrace innovation when it makes sense for the business, but not chase after every new technology that catches their eye.
David sees a future where leaders, such as the business owners who have a big share of manufacturing in Australia, are going out and sharing ideas with people in a non-competitive arena.
“Innovation for me is just about finding a mutual appetite to pursue a new idea together. And if you can do that you can harness the power of many people in one place and create some magic.”
A leader isn’t great just because they develop great strategic plans. Great manufacturing leaders must also be willing and able to make decisions. They’re also prepared to stand by them.
But overall, the best manufacturing leaders are the ones that keep their organisation engaged and focused on the right direction to achieve the company’s common vision.