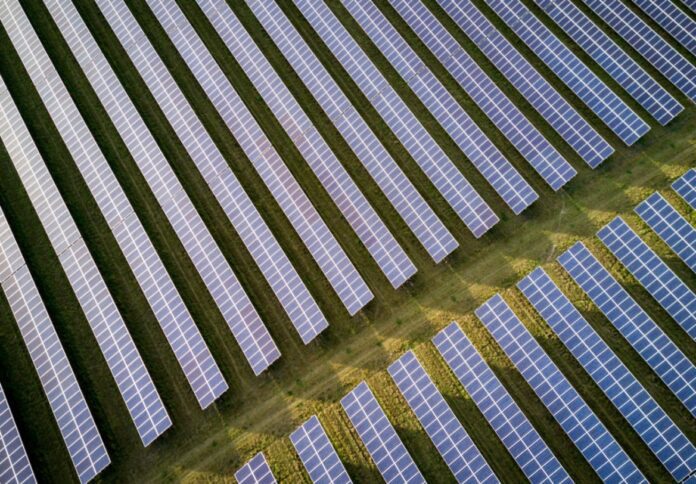
Article by Clive Jones, managing director of heat transfer fluid specialist for concentrated solar power thermal storage applications Global Heat Transfer.
Australia has led the way in rooftop solar photovoltaic (PV) penetration for the last decade — nearly one out of three Australian homes now have solar panels on their roofs, according to SunWiz.
To increase its solar power capacity, the country is investing in larger concentrated solar power (CSP) plants, including VS1, Australia’s first commercial scale CSP facility. Here, Clive Jones, managing director of heat transfer fluid specialist for concentrated solar power thermal storage applications Global Heat Transfer, explains how plant managers can improve the efficiency and extend the lifespan of their CSP technology with thermal fluid maintenance.
Thanks to reduced manufacturing, maintenance and installation costs, Australians have embraced solar power as a low-cost energy source. Many solar farms are popping up across the country, including the 10 gigawatt solar farm covering 30,000 acres of the Northern Territory. CSP technology is integral in running efficient solar farms such as this, with systems using reflectors to concentrate sunlight onto a receiver that contains heat transfer fluid media. The heated fluid is transported to a heat exchanger, where, as explained by the U.S. Department of Energy, it generates steam to drive a turbine and produce electricity.
Unlike steam-based systems, thermal fluid systems can be vented and will operate at atmospheric pressure, improving engineer safety. However, engineers must be ready to spot any signs of thermal fluid degradation early to ensure uptime.
Be proactive
Heat transfer media must perform at the correct temperature for extended periods. A parabolic trough has hundreds of mirrors that reflect the sunlight into one concentrated point, which can reach temperatures of over 400 degrees Celsius. Thermal energy is converted to electricity more efficiently at higher temperatures, so the media must tolerate these scorching conditions. Selecting a fluid with the best operating temperature range for the application is key to maintaining thermal stability and minimising heat loss. Additionally, with proactive maintenance and temperature control, engineers can ensure heat transfer efficiency, maximising plant uptime, and capacity, while also slowing degradation of the heat transfer material.
Similarly, engineers can ensure uptime all year round by selecting a fluid that can operate at low temperatures without freezing. Solar plant managers should ensure that the HTF has a freezing temperature lower than the site’s ambient temperature so that the plant can continue running from June to August, during winter. In solar applications, molten salts like Globaltherm® Omnistore are popular, but some applications may require synthetic fluids, like Globaltherm® Omnisol
Regular fluid sampling
Proactive fluid condition monitoring can help engineers detect any sign of degradation early, and before it impacts thermal fluid efficiency. Using a thermal fluid analysis kit to take regular samples can extend the operational life of the media and heat transfer system by detecting issues before they become serious. It can also help engineers detect changes in the viscosity, density and thermal conductivity — all symptomatic of early degradation.
Engineers can gain an accurate representation of the fluid’s condition by taking representative samples at regular intervals from a hot, closed and circulating system. After sending a sample to a thermal fluid expert for analysis, plant managers can use the data to identify any changes in fluid, such as carbon and acid levels, and intervene if needed.
Sampling can also provide valuable data and insights that enable engineers to plot fluid lifespan and anticipate potential issues in the future. For example, as the fluid reaches the end of its lifespan, there is a gradual curve that drops off sharply, often referred to as “the degradation curve”. At the beginning of this curve, engineers have a range of options to apply interventions which will restore fluid condition, helping it return to optimal efficiency.
Remote condition monitoring
In some CSP plants, one option is for engineers to implement a thermal fluid preventative maintenance programme, such as Thermocare® 24/7 Live Condition Monitoring, a cloud-based remote monitoring system that allows engineers to continuously monitor thermal fluid condition in real time.
The technology enables engineers to connect fluid data to the cloud, and measure a variety of parameters, including the presence of degradation factors, such as the ingress of water and other contaminants, a change in viscosity, and a drop in pressure and flow. As well as this, these programmes can detect issues that would otherwise lead to the build-up of carbon in CSP plants, including sudden temperature spikes. The platform also warns maintenance personnel by sending an alert on their smart devices if an issue is detected.
Australia’s solar switchover shows no signs of slowing down, and CSP is playing a key role in this journey. With thermal fluids central to these systems, maintenance engineers and solar plant managers take proactive steps to extend their operational lifespan — including taking regular samples for analysis and using remote condition monitoring.
Global Heat Transfer’s consultants can offer technical support and consultation for concentrated solar power and thermal storage applications. For specialised advice, contact Global Heat Transfer.
The content of this article is based on information supplied by the author. Please consult a licenced and/or registered professional in this area before making any decisions based on the content of this article.