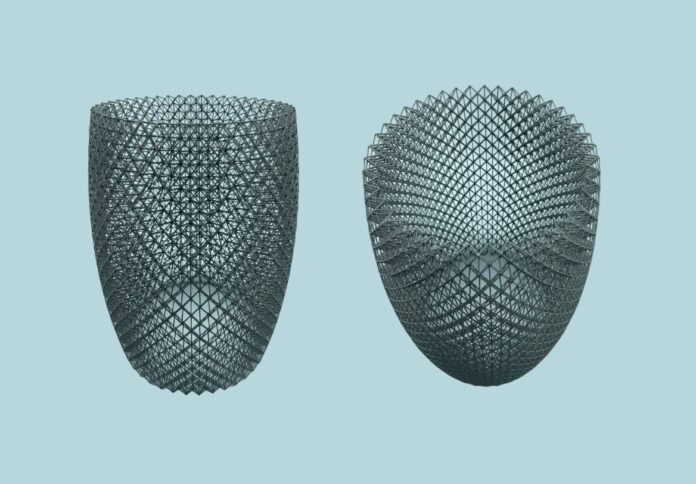
England-based metal additive manufacturer Wayland Additive is taking centre stage at Formnext 2023 with a showcase of parts crafted from challenging metals, including titanium, carbon steel, and tungsten.
Visitors attending the event, to be held from 7 to 10 November, will have the opportunity to explore Wayland’s Calibur3 metal AM system at booth B139 in Hall 12, the company said in a press release.
The exhibit will feature an array of components produced using this innovative machine, while experts from Wayland will be available for in-depth discussions about how Calibur3 is redefining the landscape of metal additive manufacturing.
In particular, Calibur3 was developed to address the common challenges associated with metal additive manufacturing.
It harnesses the benefits of metal electron beam (eBeam) powder bed fusion (PBF) technology while surmounting traditional limitations.
One standout achievement is the implementation of the fully neutralised NeuBeam process within Calibur3, which resolves issues related to charging that have previously hindered electron beam melting (EBM) processes. Crucially, the system also offers compatibility with a broader spectrum of metal materials.
Will Richardson, CEO at Wayland, affirmed, “As we champion the wider adoption of metal AM throughout the industry, our focus on extending the material range available to companies is fundamental, and this is why at Formnext 2023, it is material processing and the open nature of our metal AM systems that is front and centre.”
According to him, NeuBeam opens up numerous opportunities in complex metal production that present challenges for current metal additive manufacturing methods.
It achieves this by being compatible with a broader spectrum of metal powders, including refractory metals and highly reflective alloys.
“The importance of this cannot be overstated as for industrial users of metal AM, the issue of materials is one that is consistently seen as a bugbear. Metal AM advocates are generally very keen on the advantages that metal AM processes can offer, but they invariably want these advantages with a known material quantity/quality that they trust,” Richardson explained.
Unfortunately, many AM processes necessitate the use of new alloy variations specifically tailored for AM, resulting in a dual challenge involving unfamiliar processes and materials.
Thus, NeuBeam’s innovation lies in its ability to work with existing metal materials, reducing the complexities associated with validating new components.
Richardson explained, “The elimination of residual stresses is a huge opportunity for the accelerated uptake of metal AM across a whole array of industry applications which we are eager to discuss with visitors at this year’s Formnext. It is fundamentally because of the fact that the process is what we call a ‘hot part’ rather than a ‘hot bed’ process.”
At the Formnext booth, attendees will observe intricate large components manufactured from various materials.
For instance, when processed with NeuBeam, titanium parts do not necessitate additional heat treatment after printing.
Additionally, the NeuBeam process enables the printing of carbon steel alloys with higher carbon content, which would typically result in cracking when using traditional laser powder bed fusion (PBF) methods.