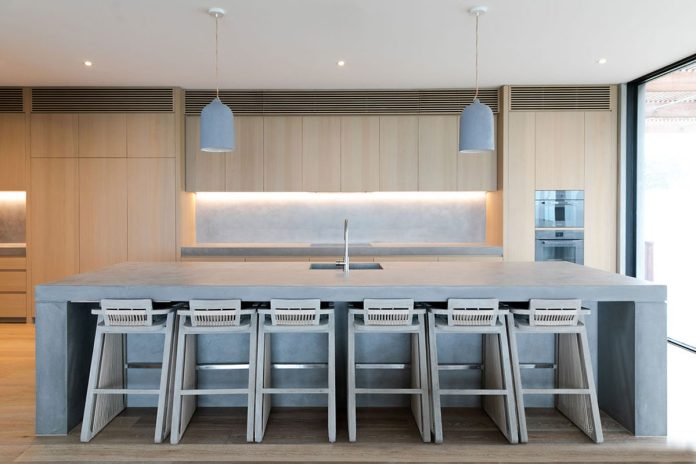
Concrete Collective uses the Fusion 360 Nesting & Fabrication Extension to cut the melamine board for their molding accurately and cost-effectively, resulting in beautiful bespoke designs.
Concrete Collective uses the Fusion 360 Nesting & Fabrication Extension to cut the melamine board for their molding accurately and cost-effectively, resulting in beautiful bespoke designs.